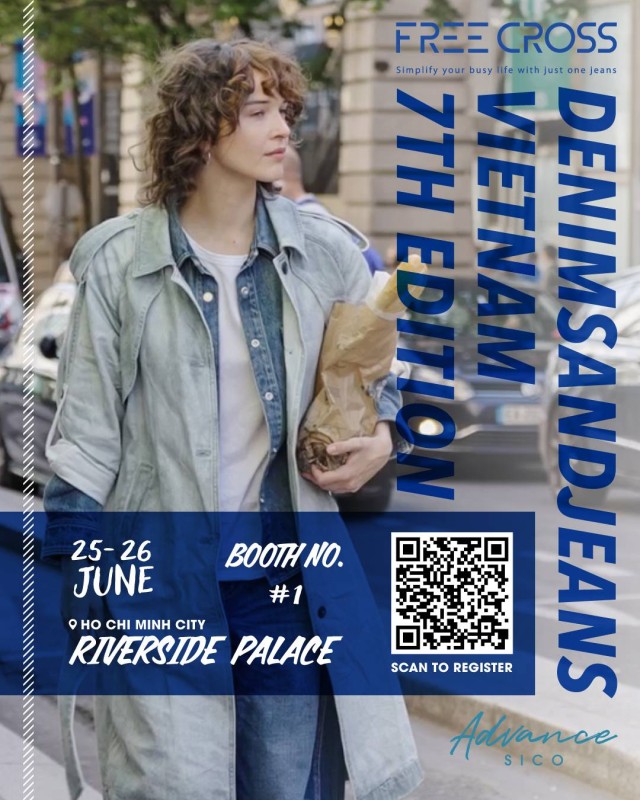
Denimsandjeans Vietnam Show 7th Edition
25 June 2025
25 June 2025
Explore
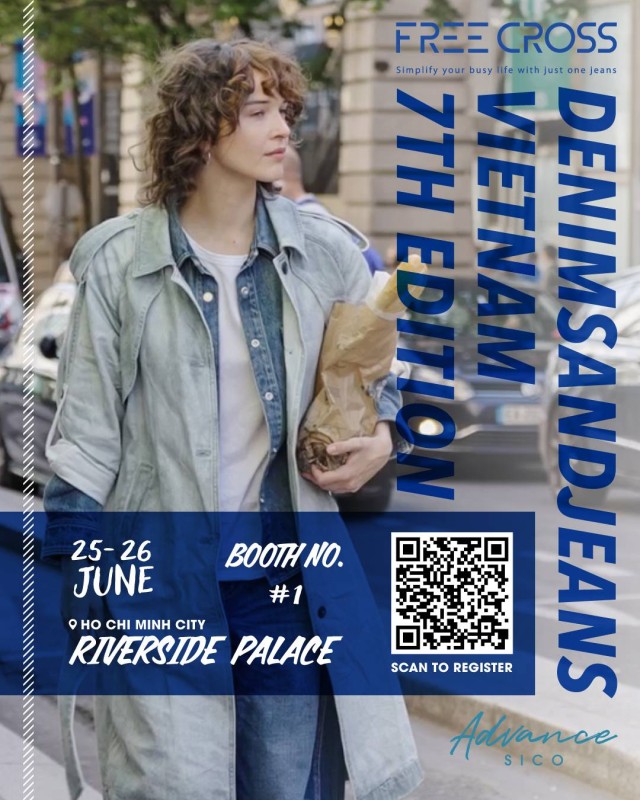
Denimsandjeans Vietnam Show 7th Edition
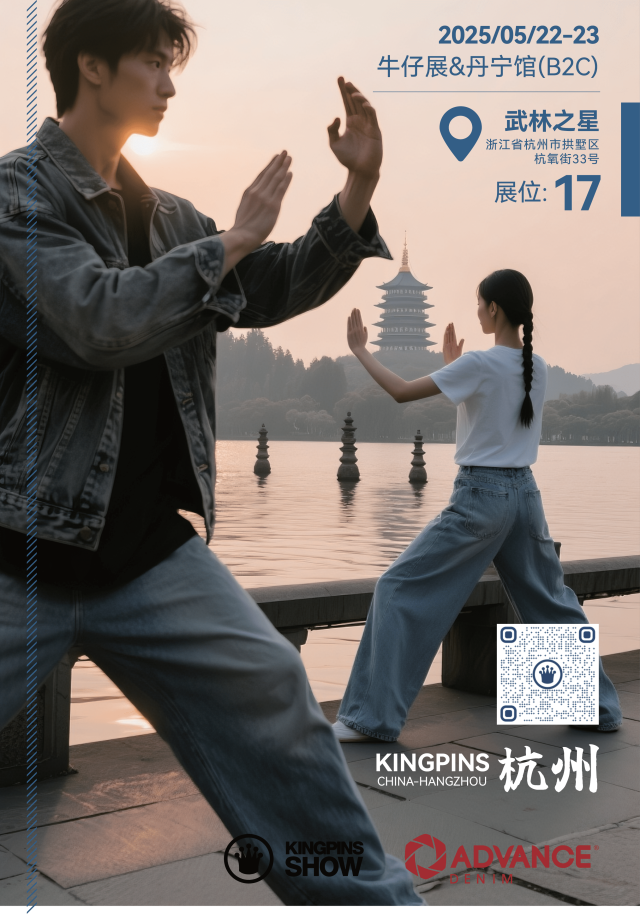
Kingpins Show in HangZhou China
22 May 2025
22 May 2025
Explore
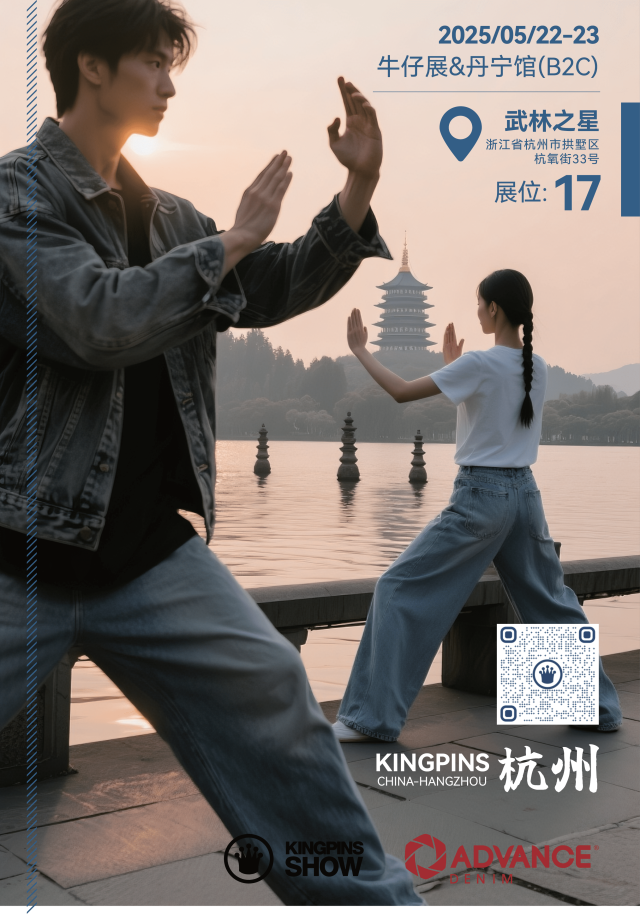
Kingpins Show in HangZhou China
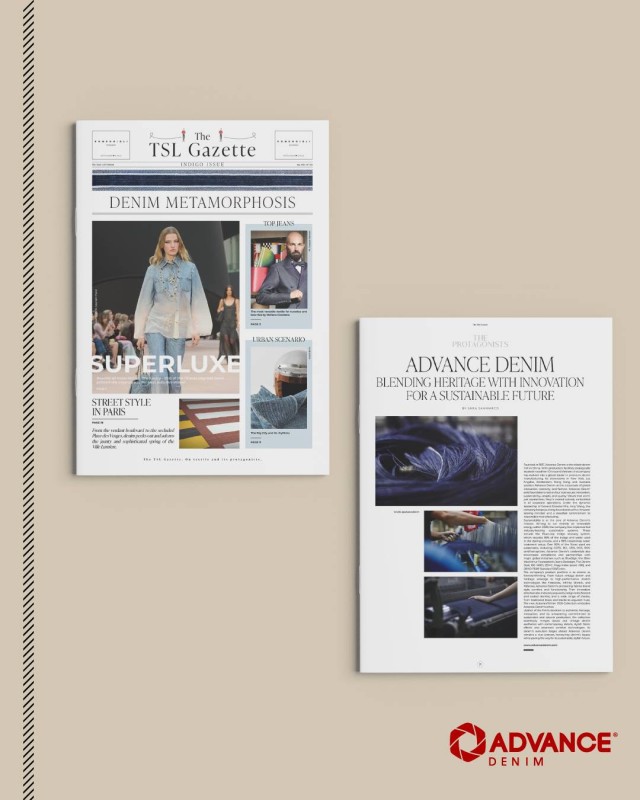
ADVANCE DENIM BLENDING HERITAGE WITH INNOVATION FOR A SUSTAINABLE FUTURE
26 May 2025
26 May 2025
Explore
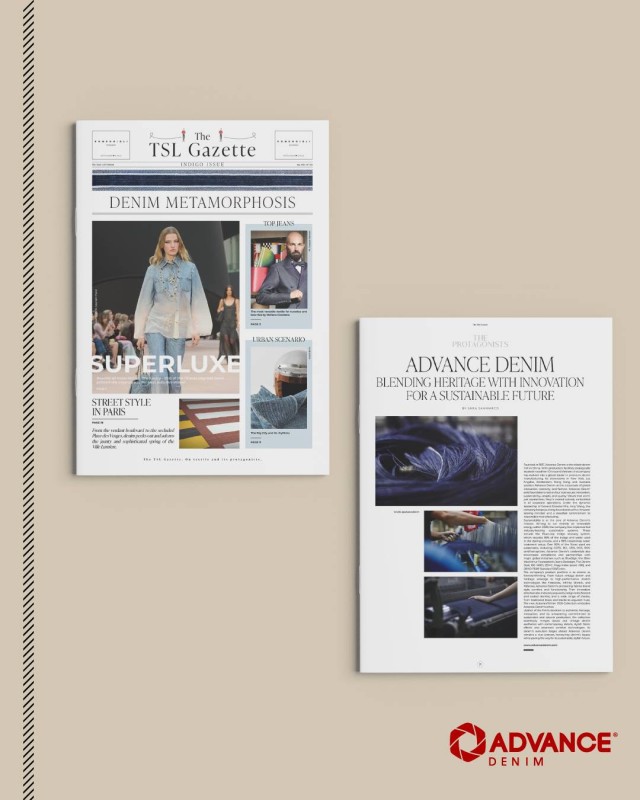
ADVANCE DENIM BLENDING HERITAGE WITH INNOVATION FOR A SUSTAINABLE FUTURE
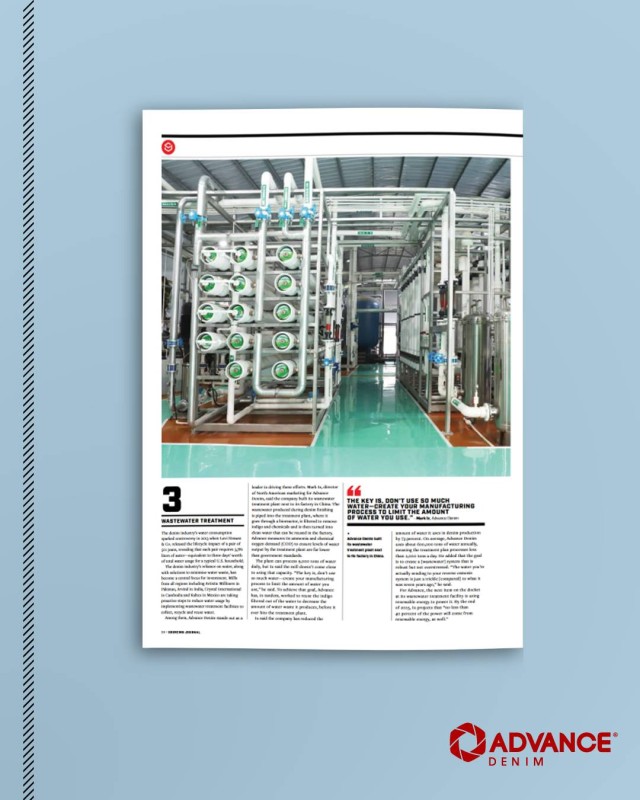
Advance Denim Stands Out as the Leader in Driving Wastewater Treatment Efforts
20 May 2025
20 May 2025
Explore
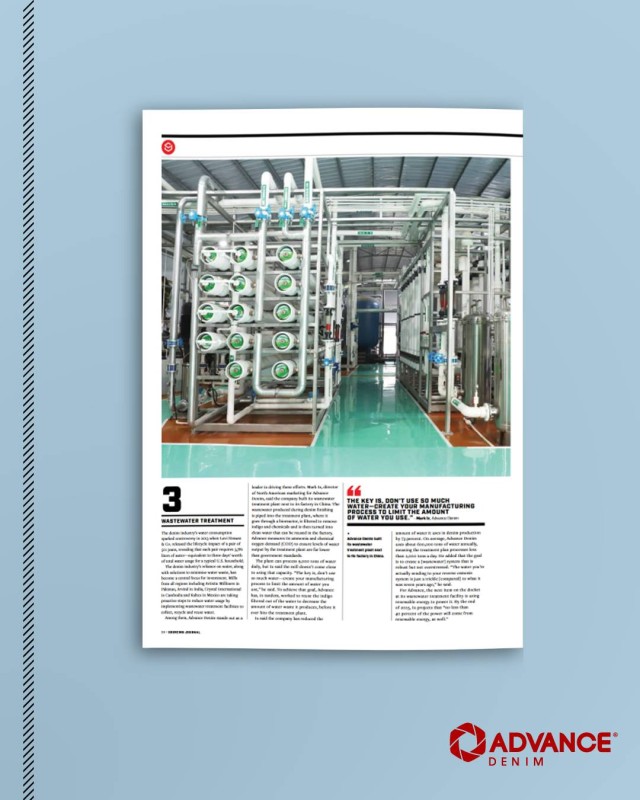
Advance Denim Stands Out as the Leader in Driving Wastewater Treatment Efforts
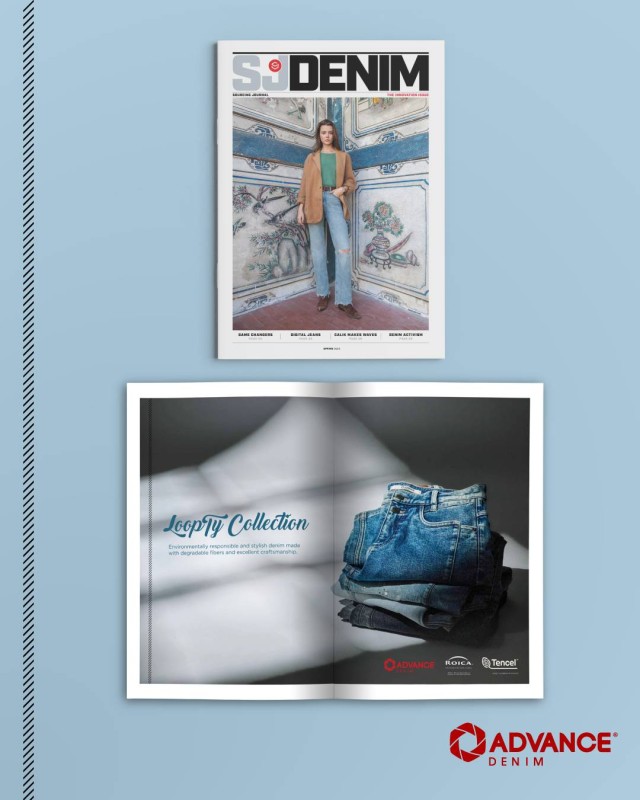
LoopTy Collection – A Collaborative Innovation by Advance Denim, ROICA™ & Lenzing
19 May 2025
19 May 2025
Explore
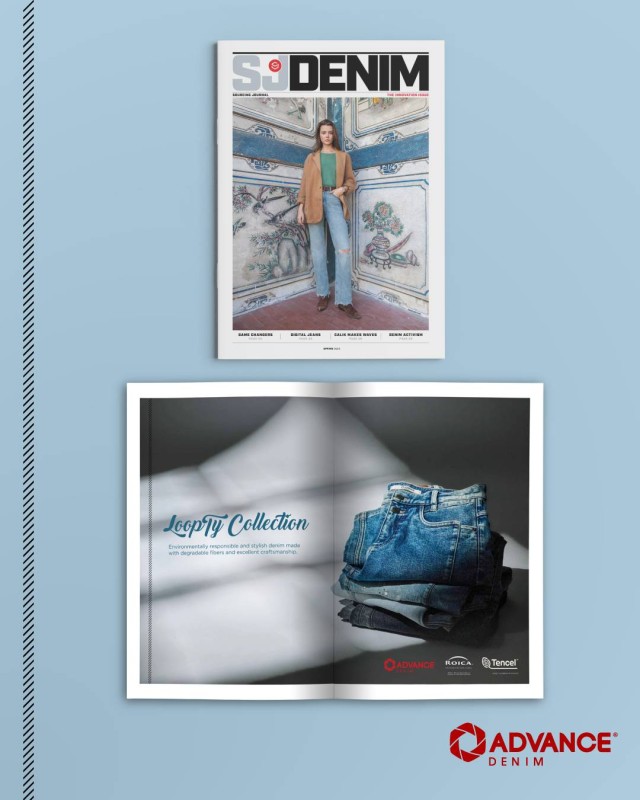
LoopTy Collection – A Collaborative Innovation by Advance Denim, ROICA™ & Lenzing
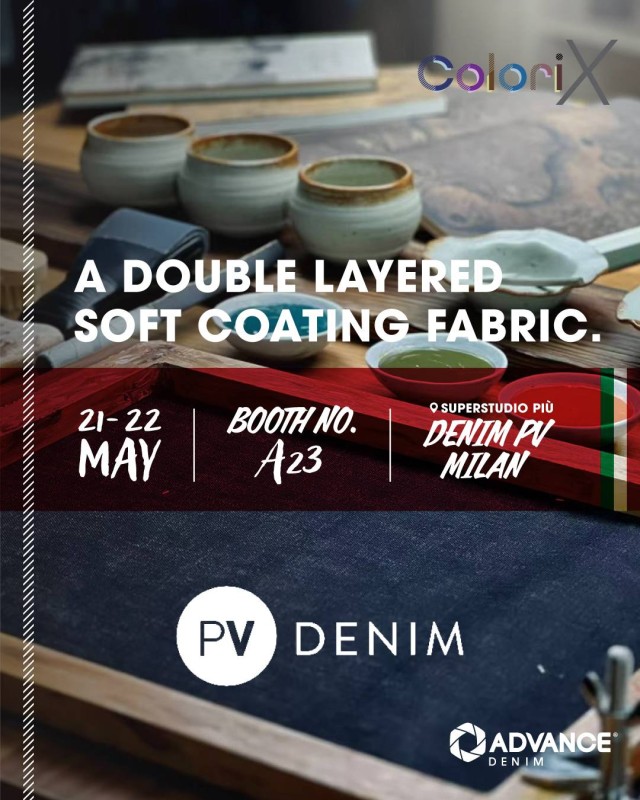
DENIM PREMIÈRE VISION IN MILAN
21 May 2025
21 May 2025
Explore
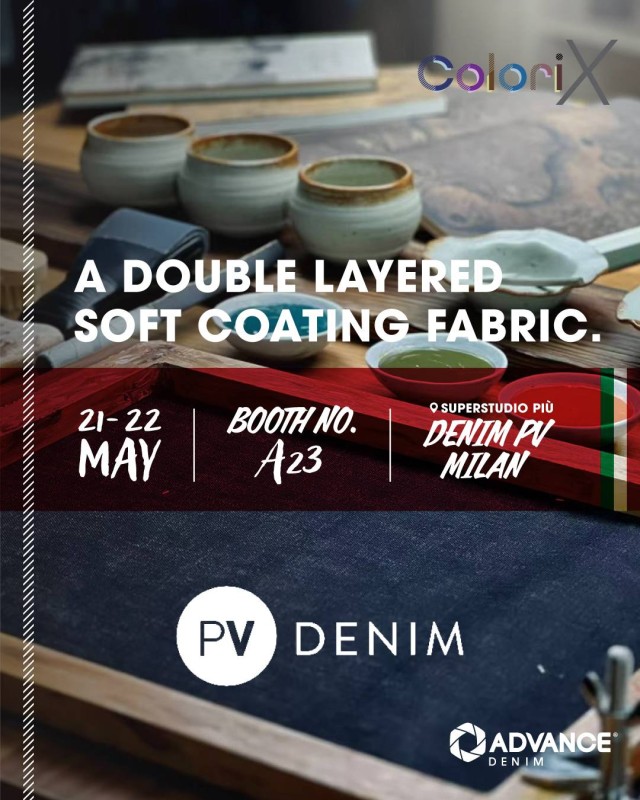
DENIM PREMIÈRE VISION IN MILAN
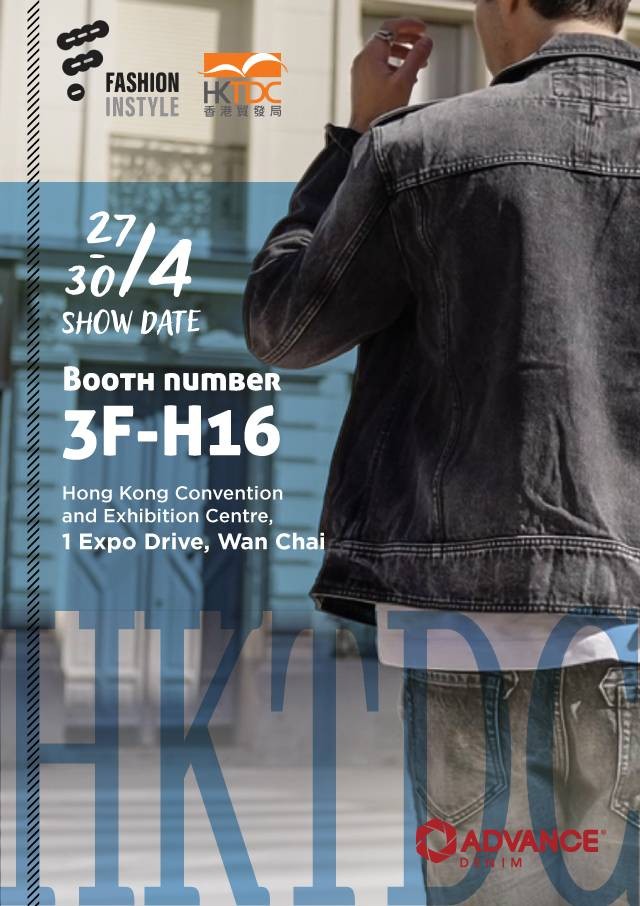
FASHION IN STYLE SHOW IN HONG KONG
26 April 2025
26 April 2025
Explore
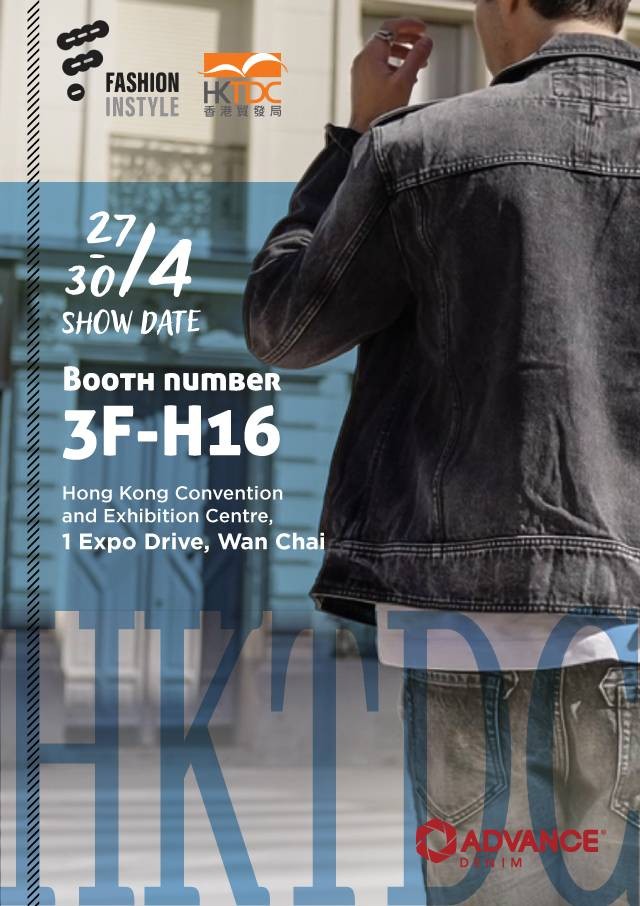
FASHION IN STYLE SHOW IN HONG KONG
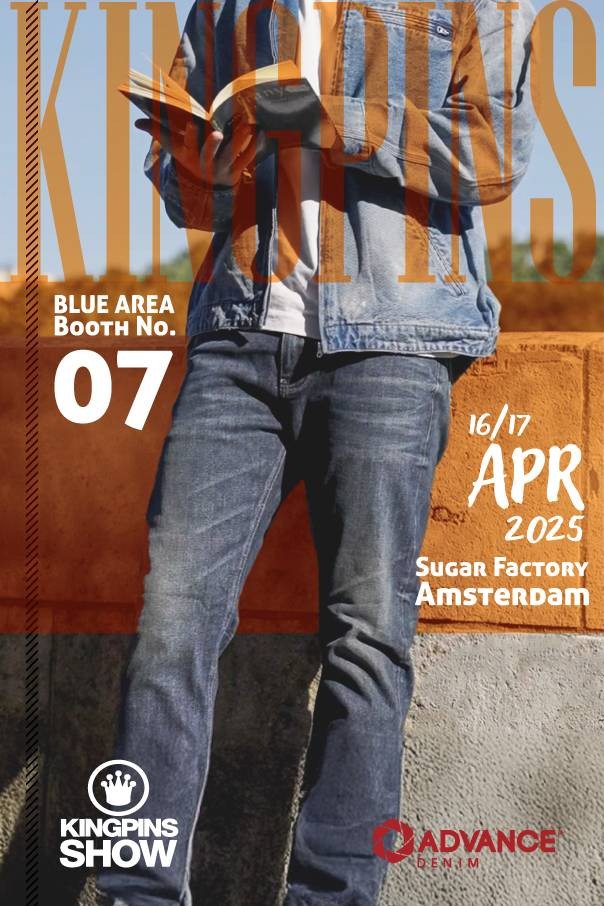
KINGPINS SHOW IN AMSTERDAM
16 April 2025
16 April 2025
Explore
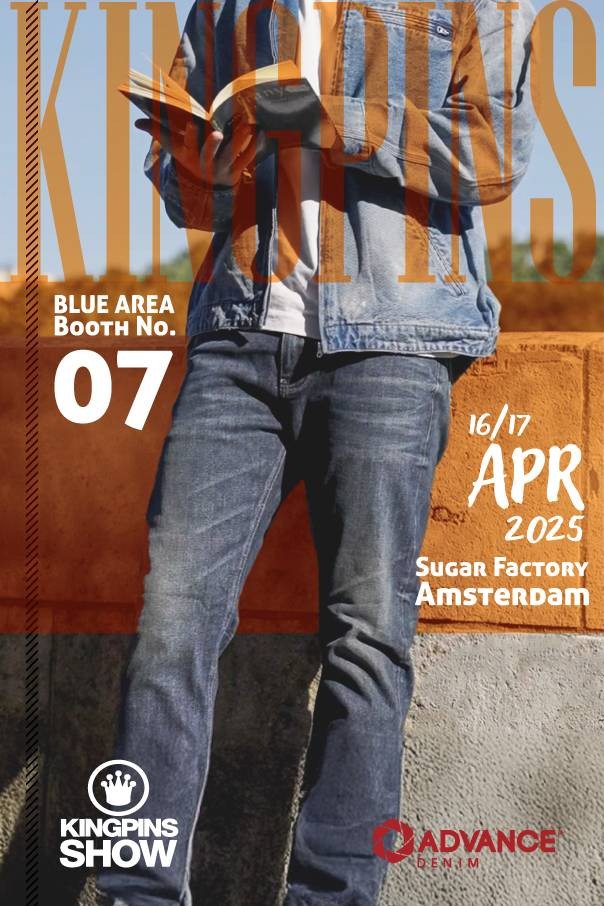
KINGPINS SHOW IN AMSTERDAM
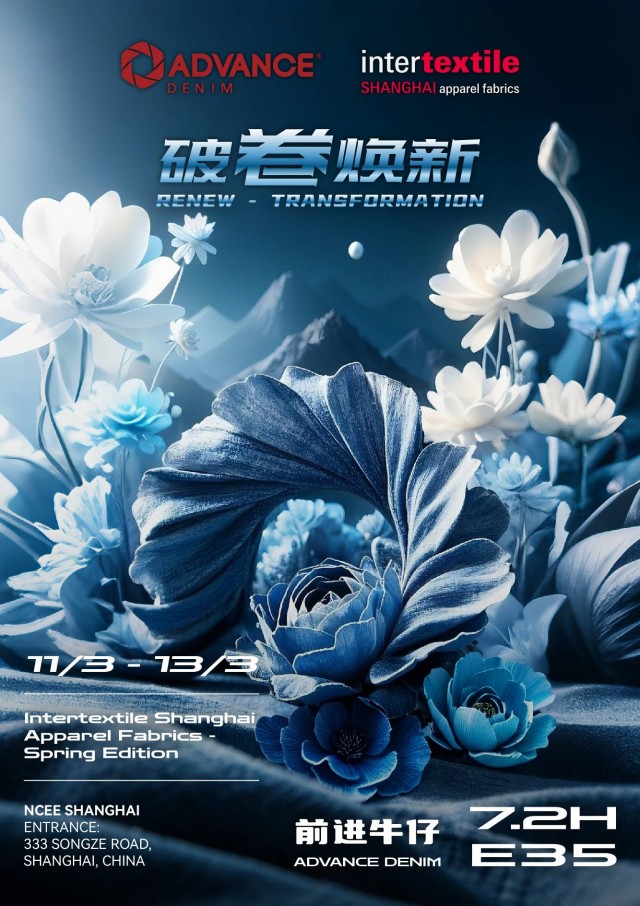
INTERTEXTILE SHANGHAI APPAREL FABRICS
11-13 March 2025
11-13 March 2025
Explore
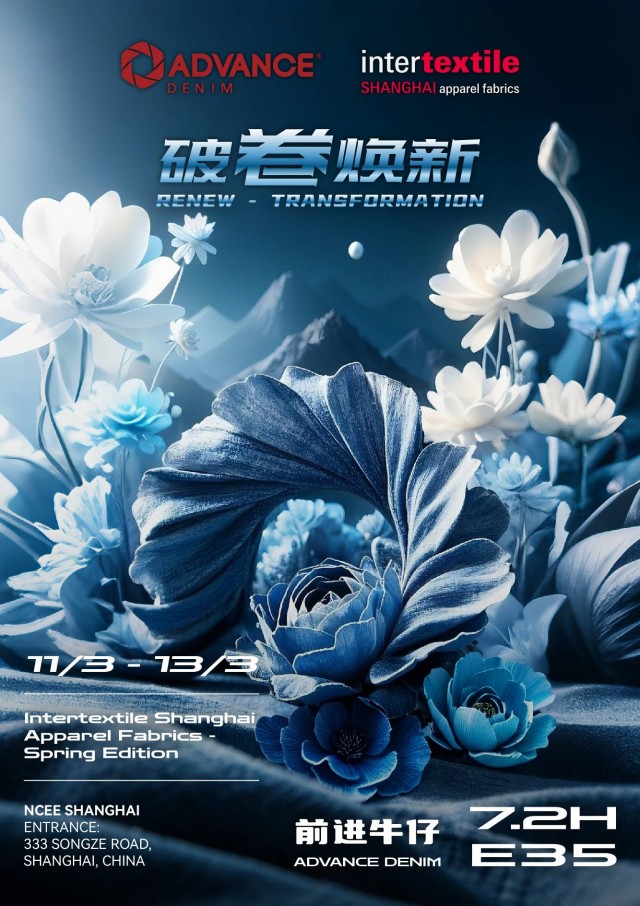
INTERTEXTILE SHANGHAI APPAREL FABRICS
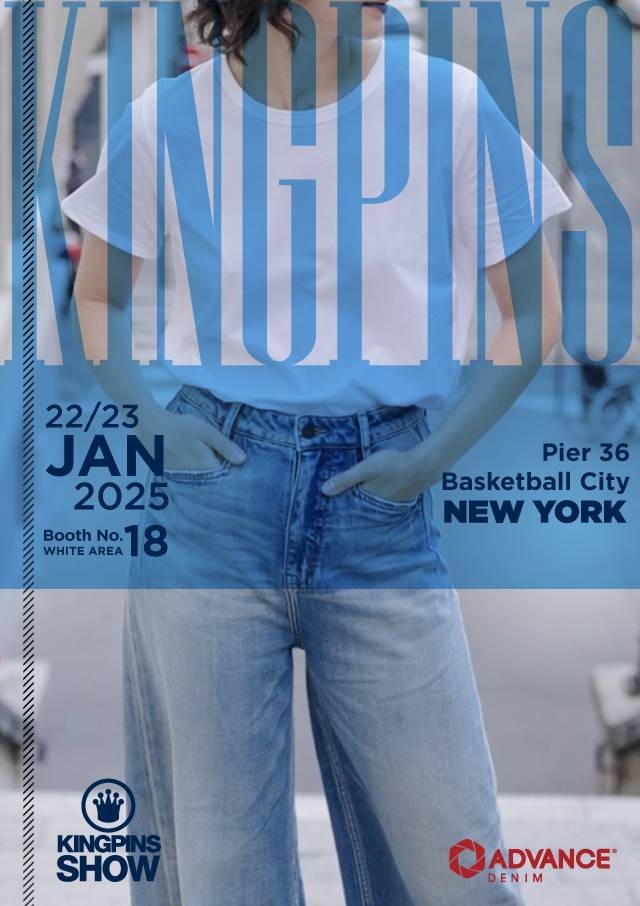
KINGPINS SHOW IN NEW YORK
17 January 2025
17 January 2025
Explore
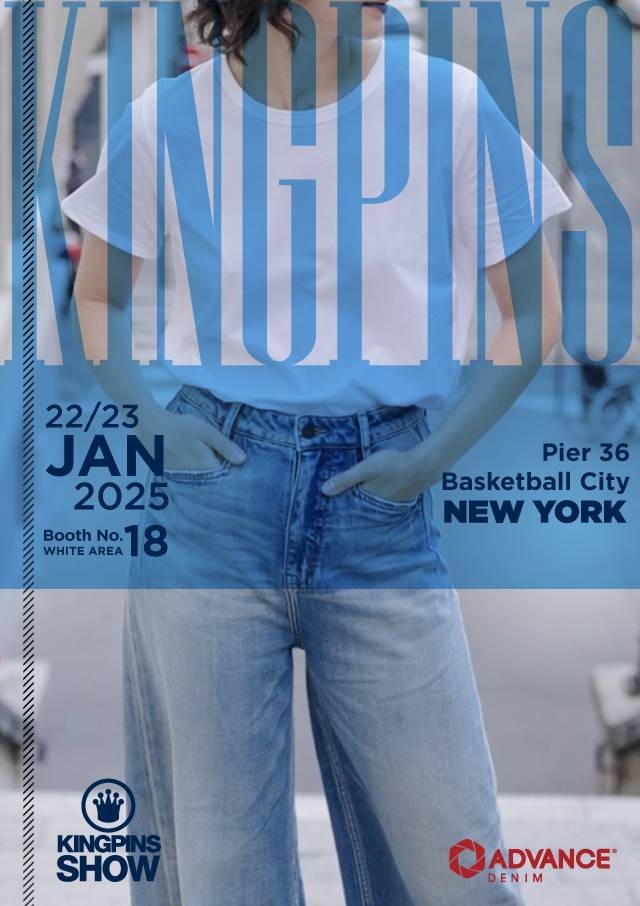
KINGPINS SHOW IN NEW YORK
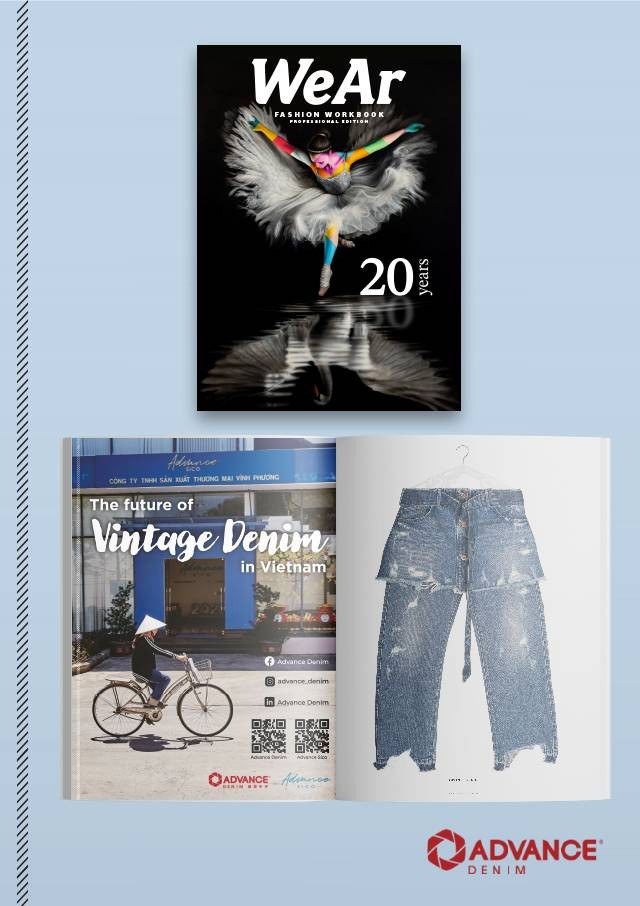
ADVANCE DENIM CUTTING -EDGE INNOVATIONS
14 November 2024
14 November 2024
Explore
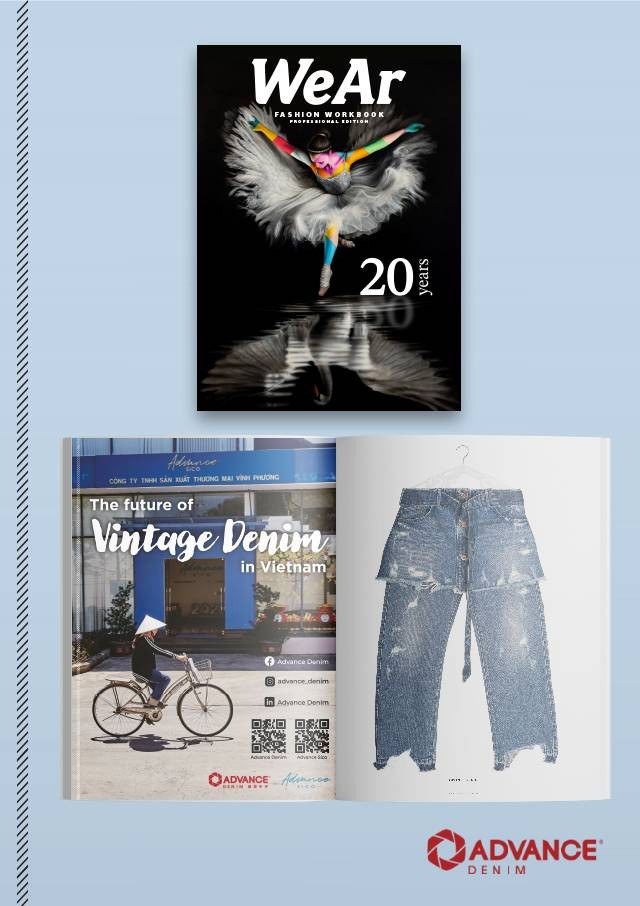
ADVANCE DENIM CUTTING -EDGE INNOVATIONS
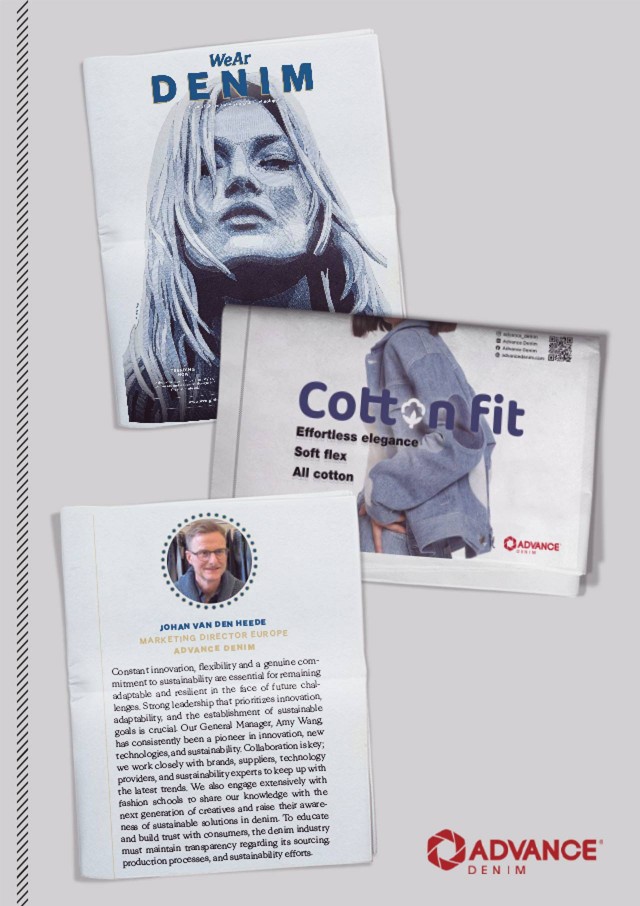
WeAr DENIM : Casual Fabrics and Sustainable Technologies
14 November 2024
14 November 2024
Explore
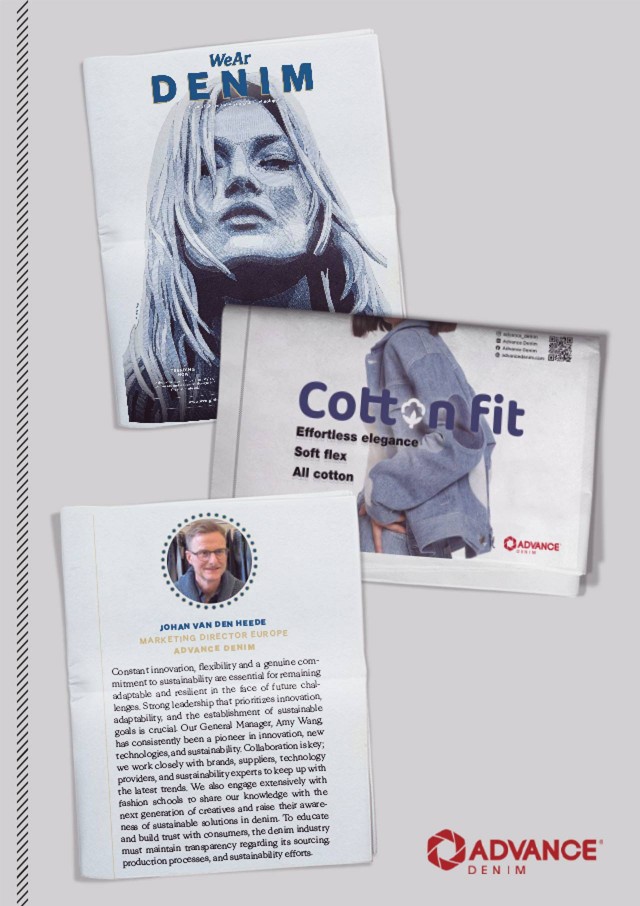
WeAr DENIM : Casual Fabrics and Sustainable Technologies
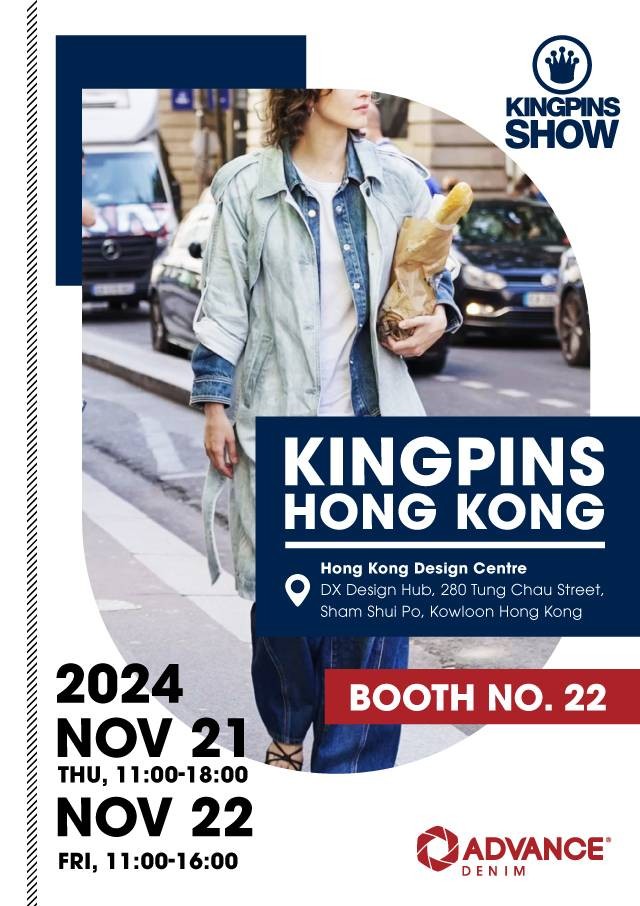
KINGPINS SHOW IN HONG KONG
21 November 2024
21 November 2024
Explore
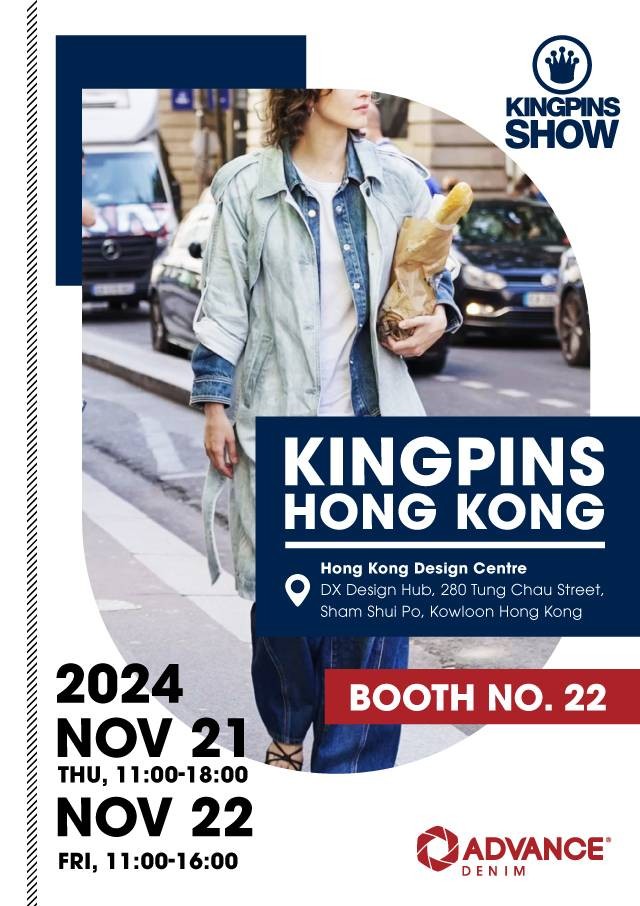
KINGPINS SHOW IN HONG KONG
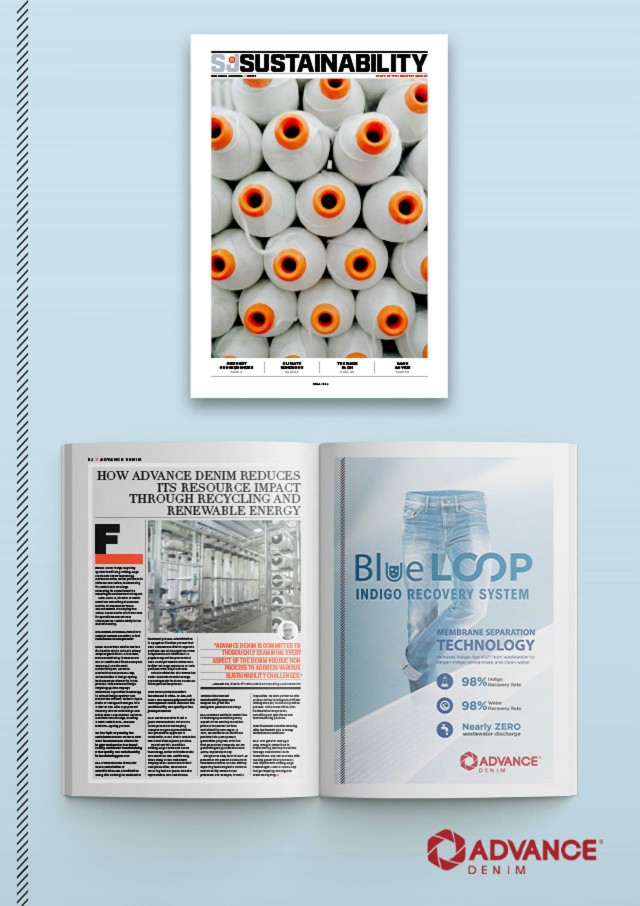
HOW ADVANCE DENIM REDUCES ITS RESOURCE IMPACT THROUGH RECYCLING AND RENEWABLE ENERGY
24 October 2024
24 October 2024
Explore
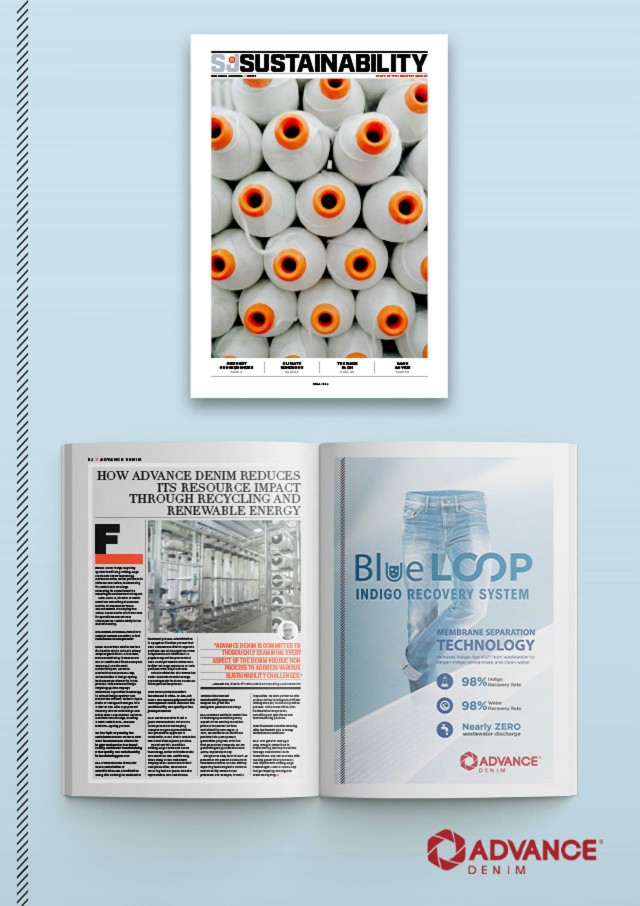
HOW ADVANCE DENIM REDUCES ITS RESOURCE IMPACT THROUGH RECYCLING AND RENEWABLE ENERGY
KINGPINS SHOW IN AMSTERDAM
17 October 2024
17 October 2024
Explore
KINGPINS SHOW IN AMSTERDAM
INTERTEXTILE SHANGHAI APPAREL FABRICS
24 August 2024
24 August 2024
Explore
INTERTEXTILE SHANGHAI APPAREL FABRICS
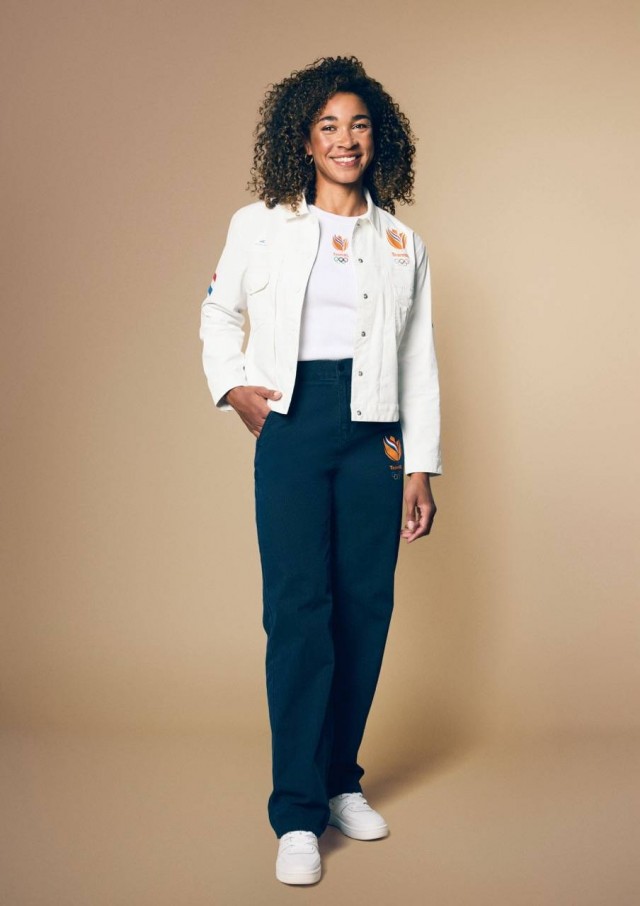
Advance Denim Collaborated with Denham to Develop TeamNL Kinetic Denim Uniform
19 July 2024
19 July 2024
Explore
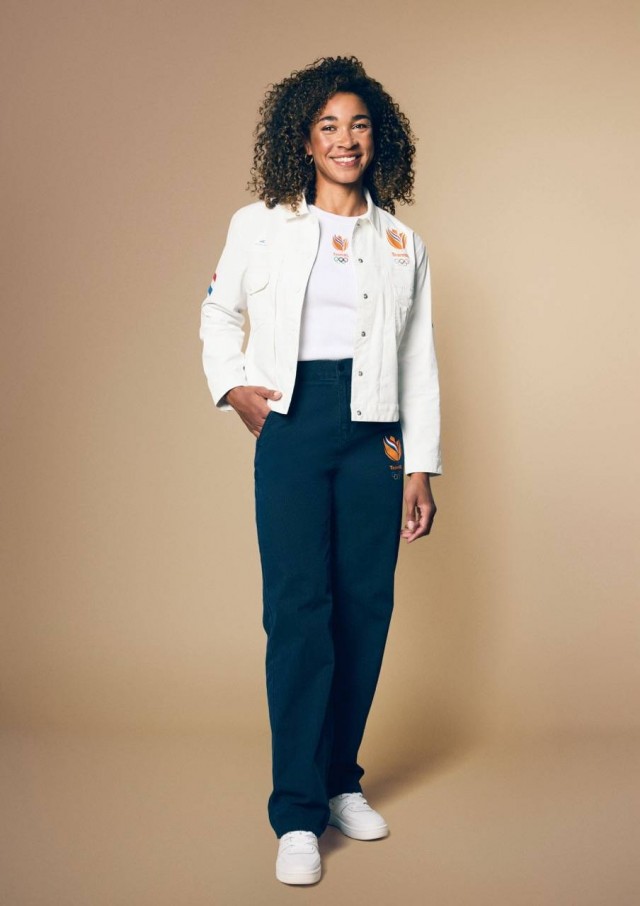
Advance Denim Collaborated with Denham to Develop TeamNL Kinetic Denim Uniform
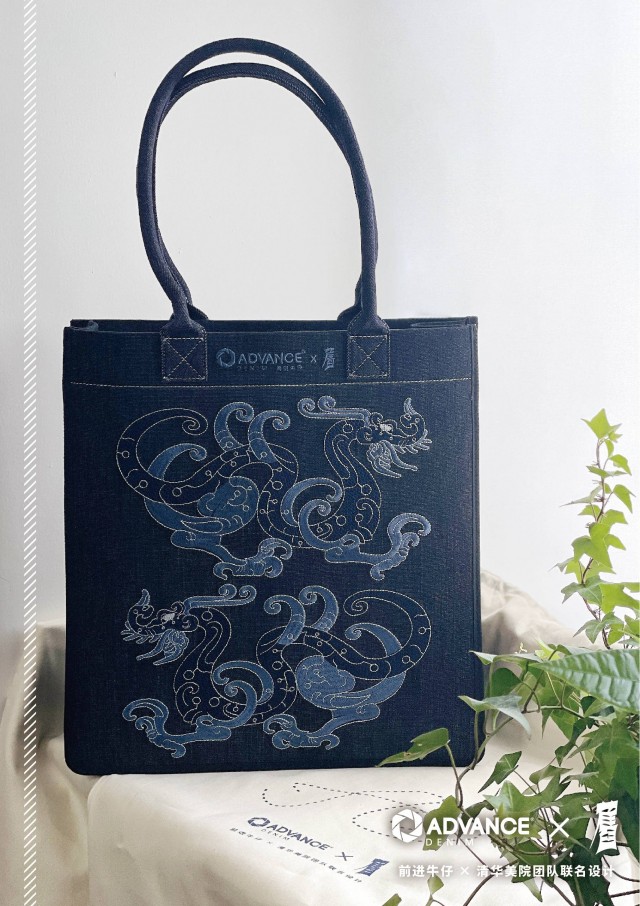
Advance Denim × Academy of Arts & Design,Tsinghua University Co-Designed Year of the Dragon Denim Bag
19 July 2024
19 July 2024
Explore
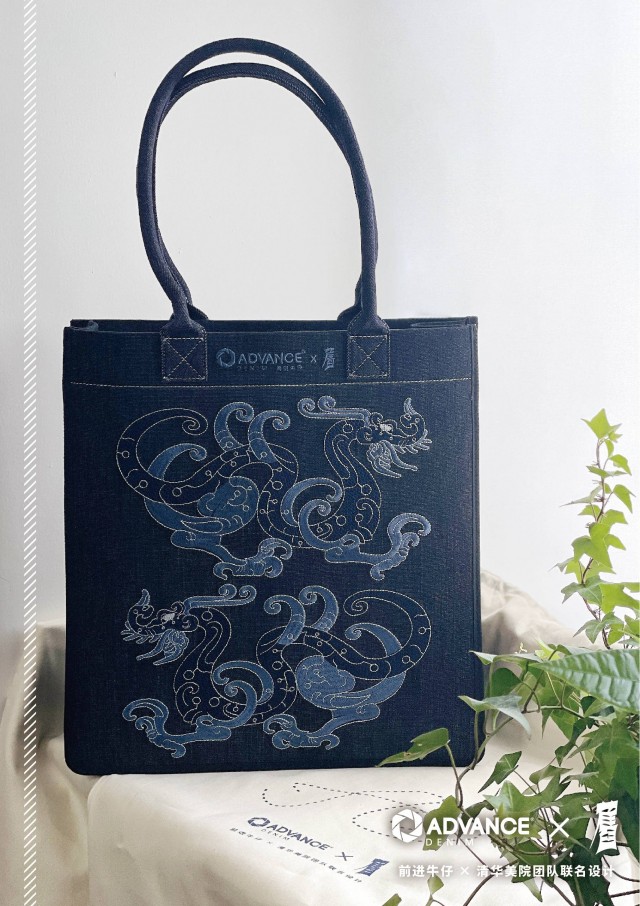
Advance Denim × Academy of Arts & Design,Tsinghua University Co-Designed Year of the Dragon Denim Bag
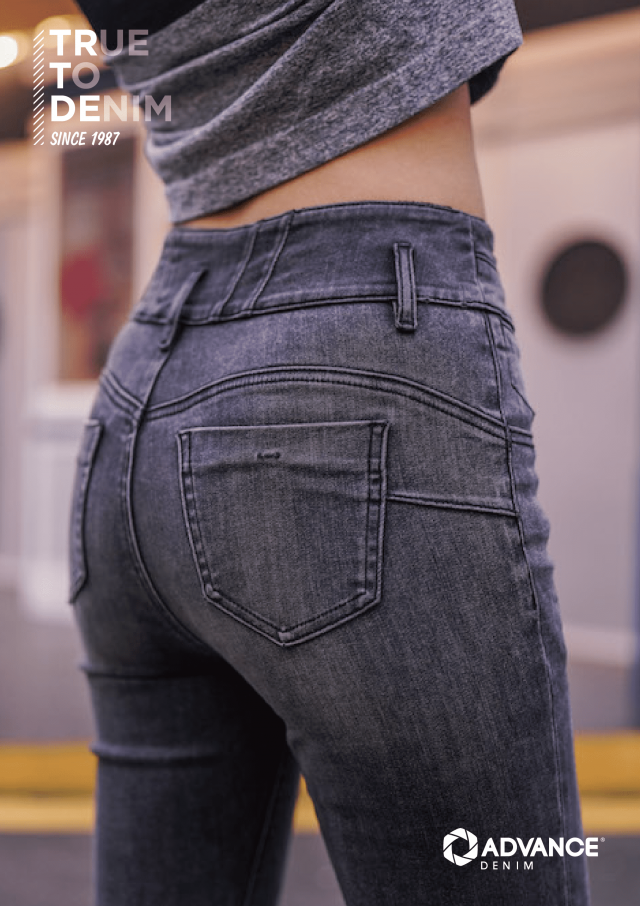
ADVANCE DENIM DELIVERS ‘TARGETED STRETCH’ WITH LAUNCH OF LYCRA FITSENSE® TECHNOLOGY
5 July 2024
5 July 2024
Explore
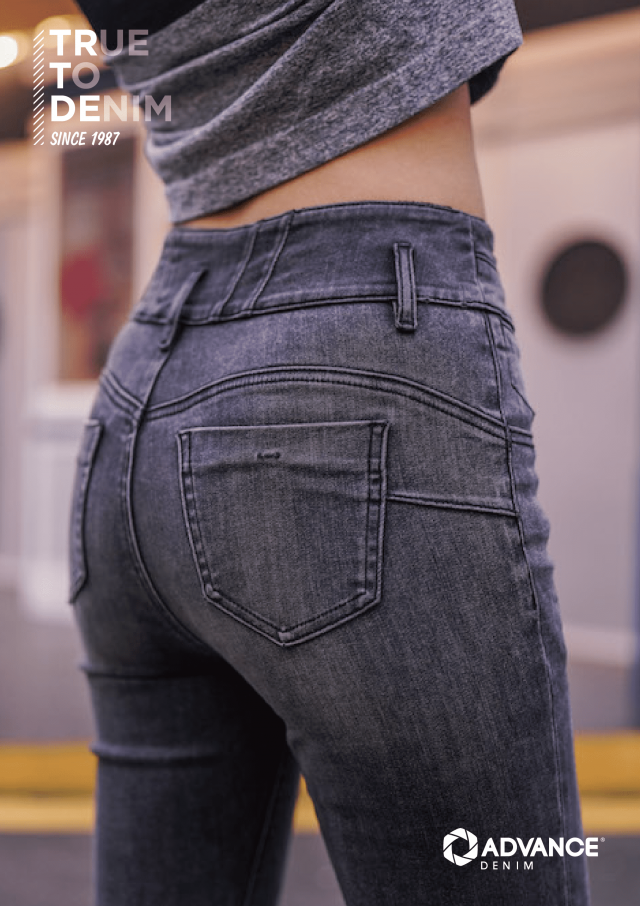
ADVANCE DENIM DELIVERS ‘TARGETED STRETCH’ WITH LAUNCH OF LYCRA FITSENSE® TECHNOLOGY
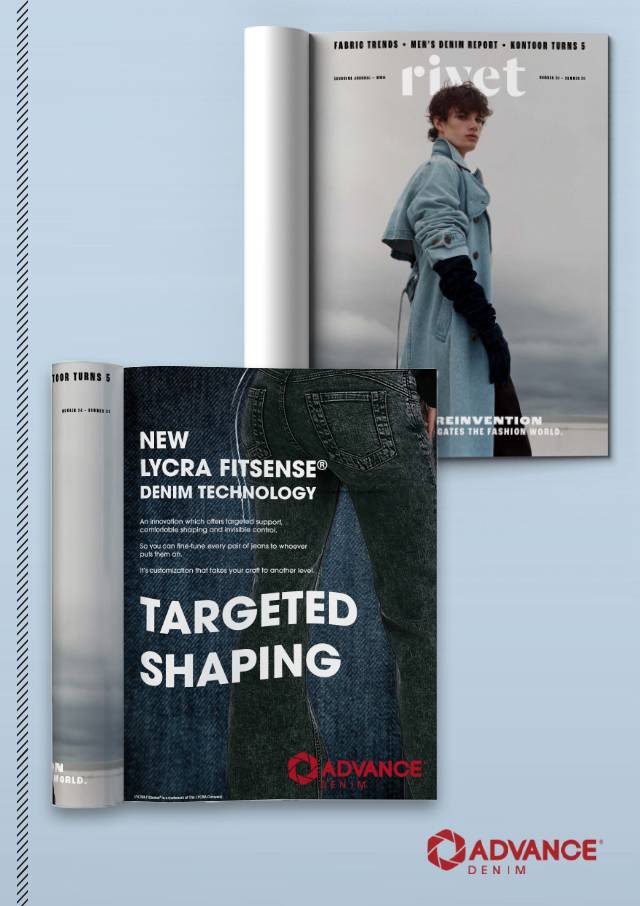
New Lycra Fitsense®️ Denim Technology
26 June 2024
26 June 2024
Explore
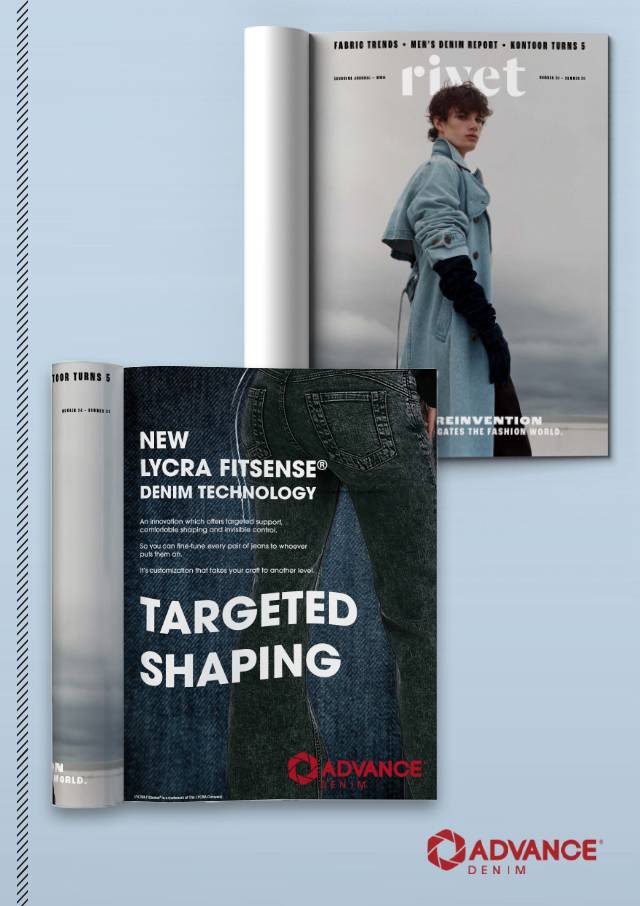
New Lycra Fitsense®️ Denim Technology
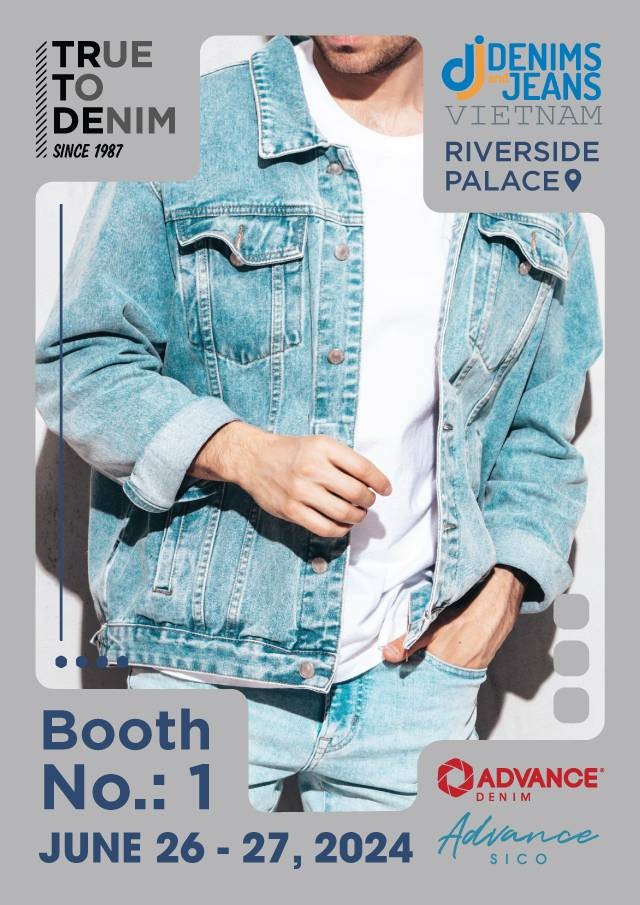
Denim and Jeans Show in Vietnam
20 June 2024
20 June 2024
Explore
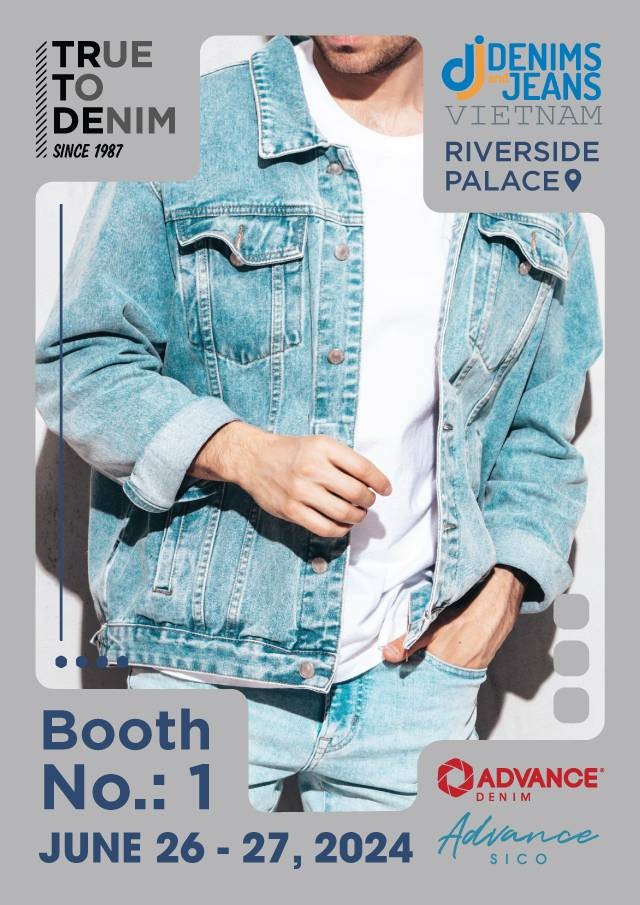
Denim and Jeans Show in Vietnam
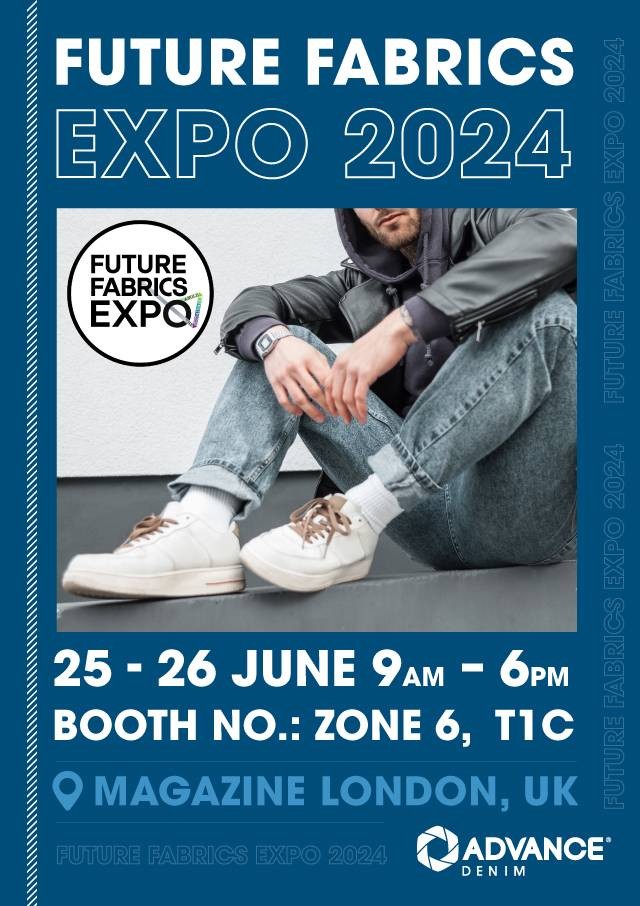
Future Fabrics Expo in London
19 June 2024
19 June 2024
Explore
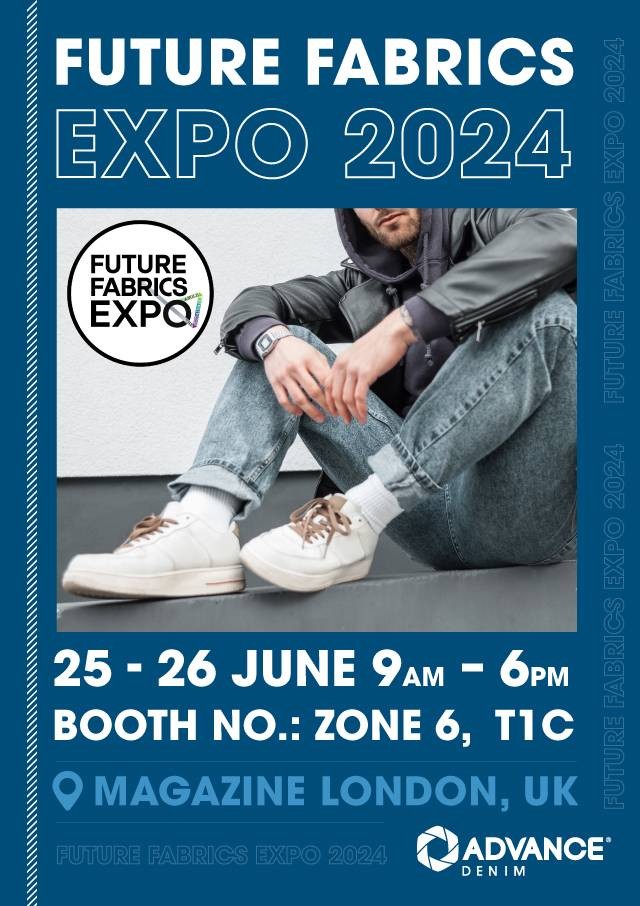
Future Fabrics Expo in London
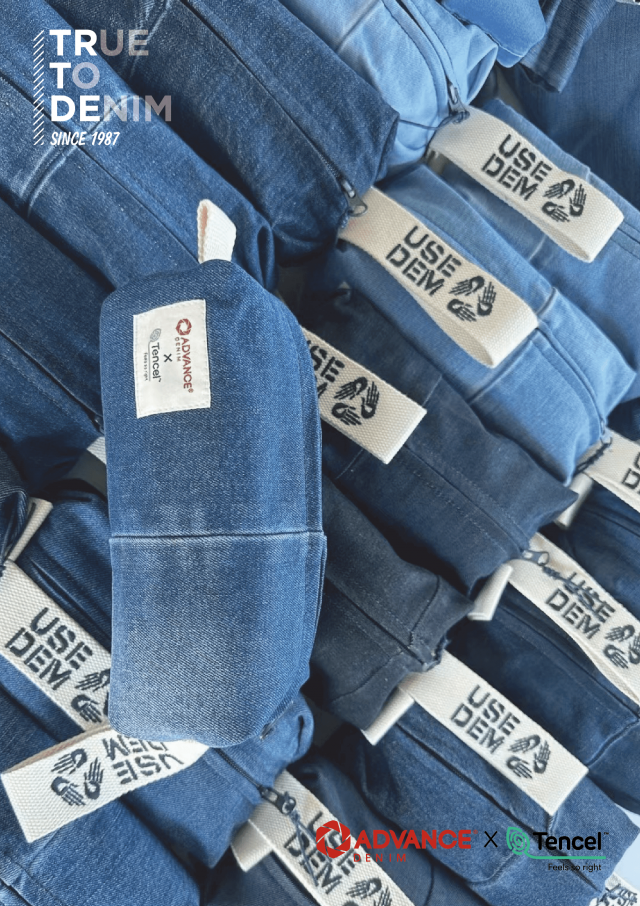
Limitless Design Solutions for Sustainable Denim
11 June 2024
11 June 2024
Explore
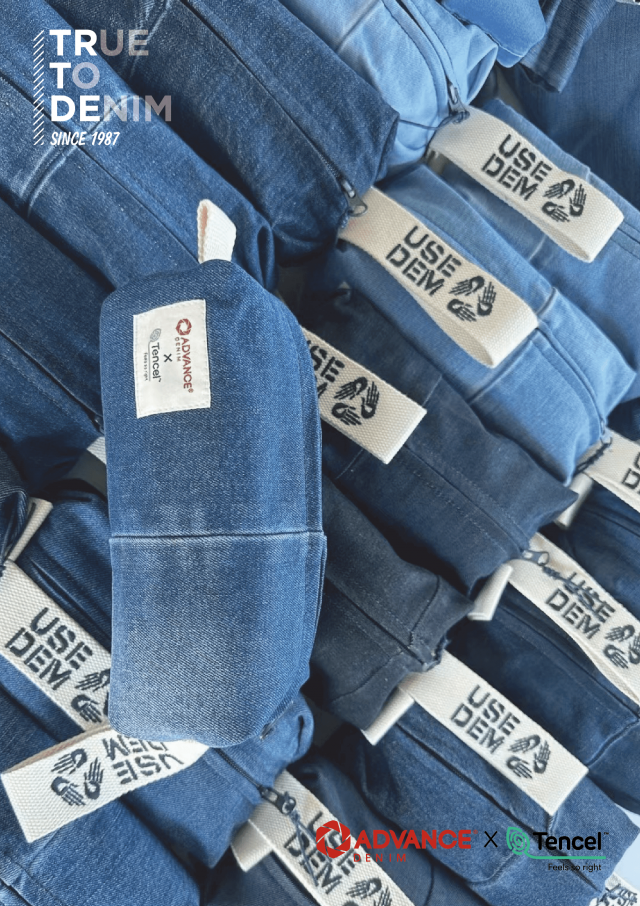
Limitless Design Solutions for Sustainable Denim
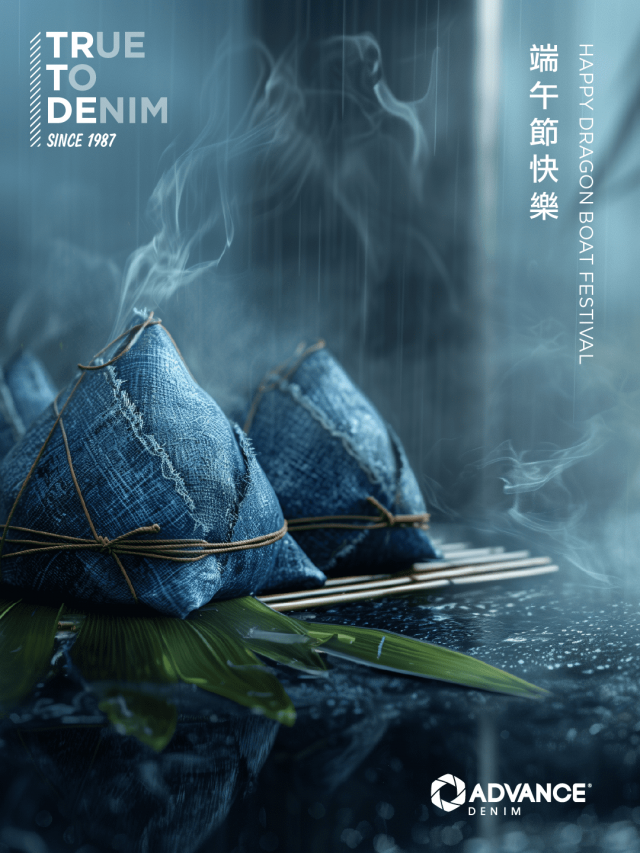
Happy Dragon Boat Festival
10 June 2024
10 June 2024
Explore
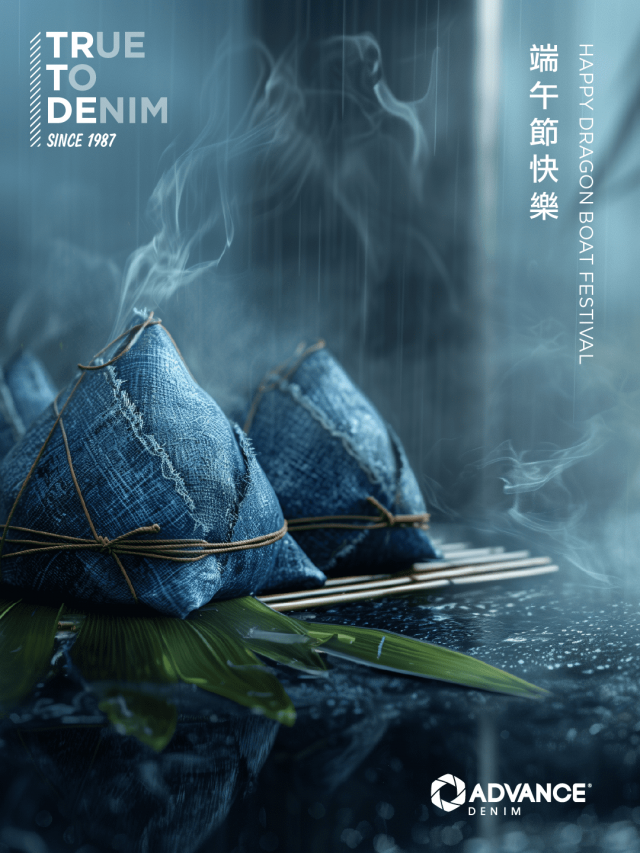
Happy Dragon Boat Festival
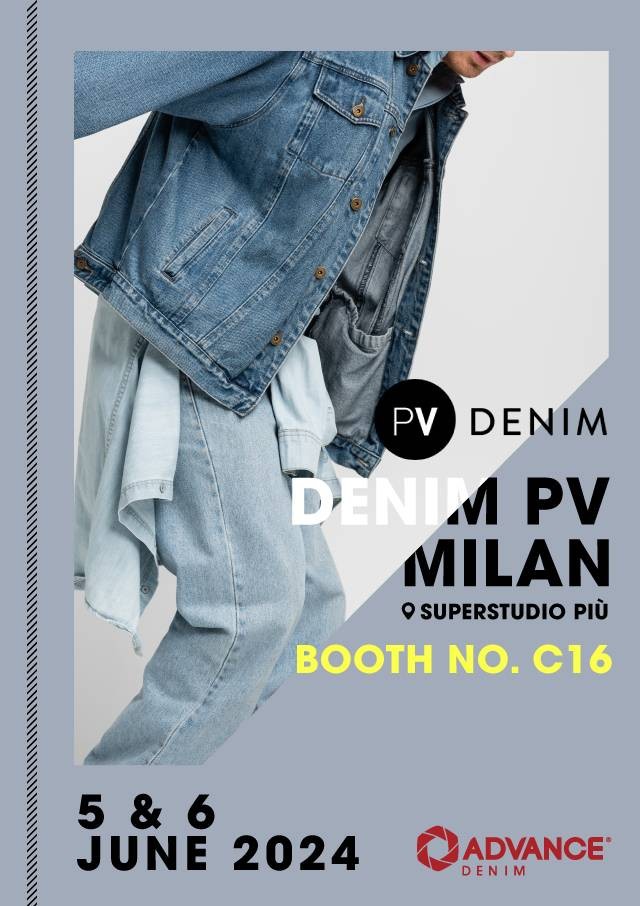
Denim Première Vision Show in Milan
1 June 2024
1 June 2024
Explore
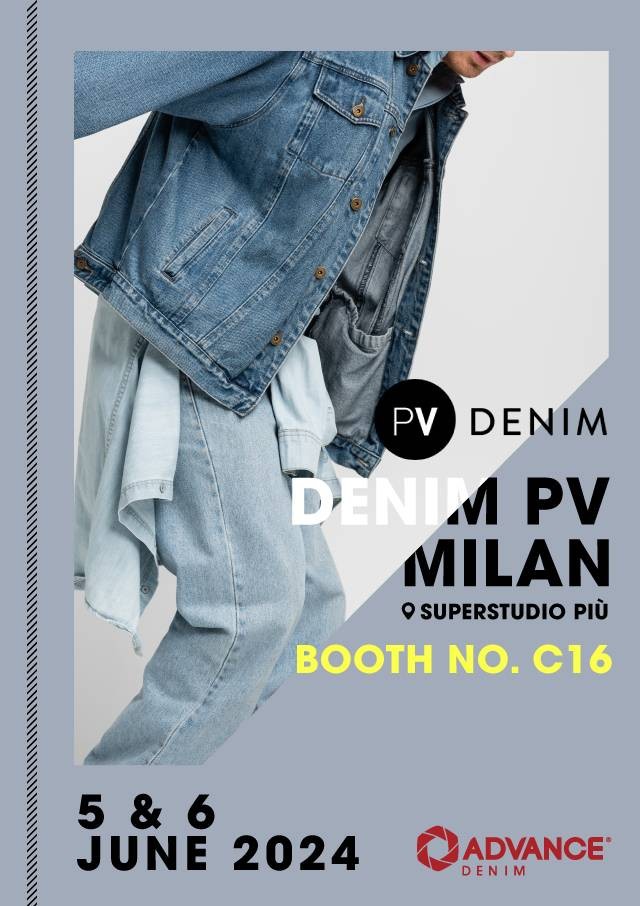
Denim Première Vision Show in Milan
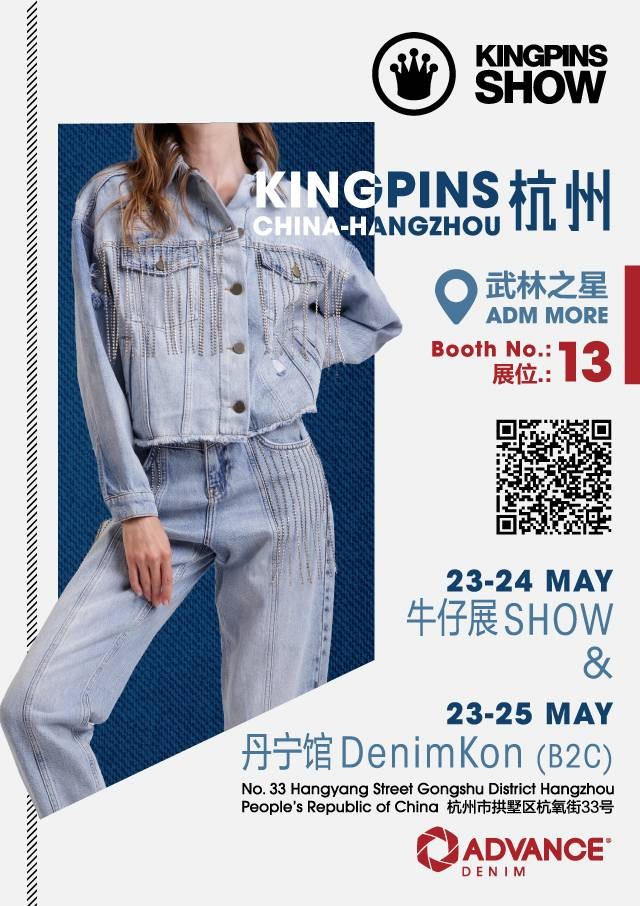
Kingpins Show in HangZhou China
20 May 2024
20 May 2024
Explore
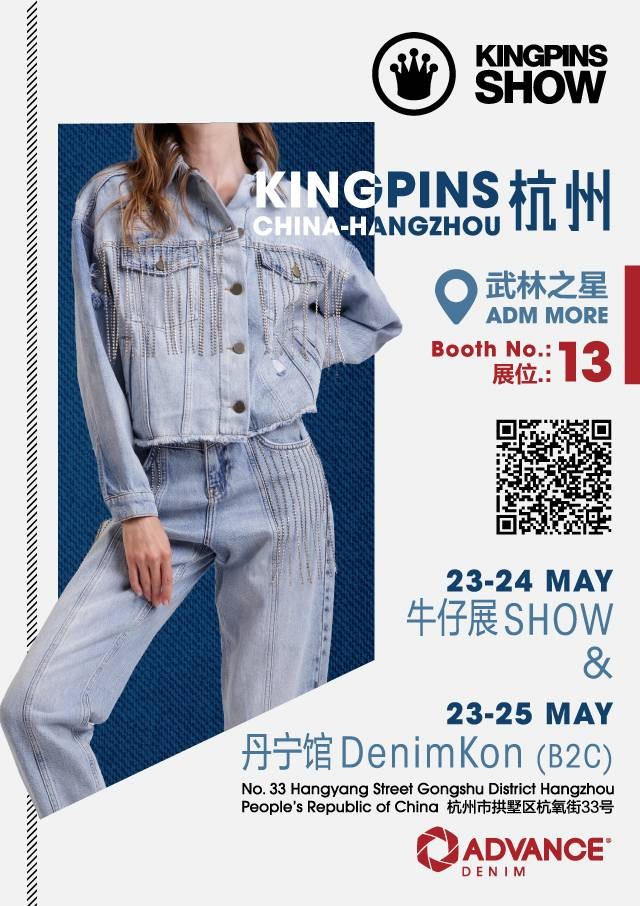
Kingpins Show in HangZhou China
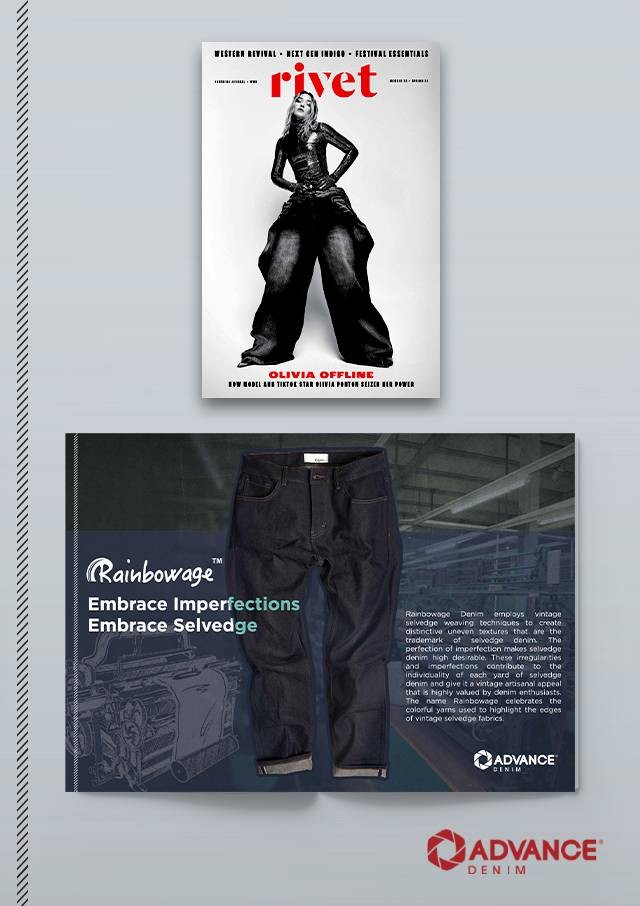
Embrace Imperfections Embrace Selvedge (Rivet Magazine)
20 April 2024
20 April 2024
Explore
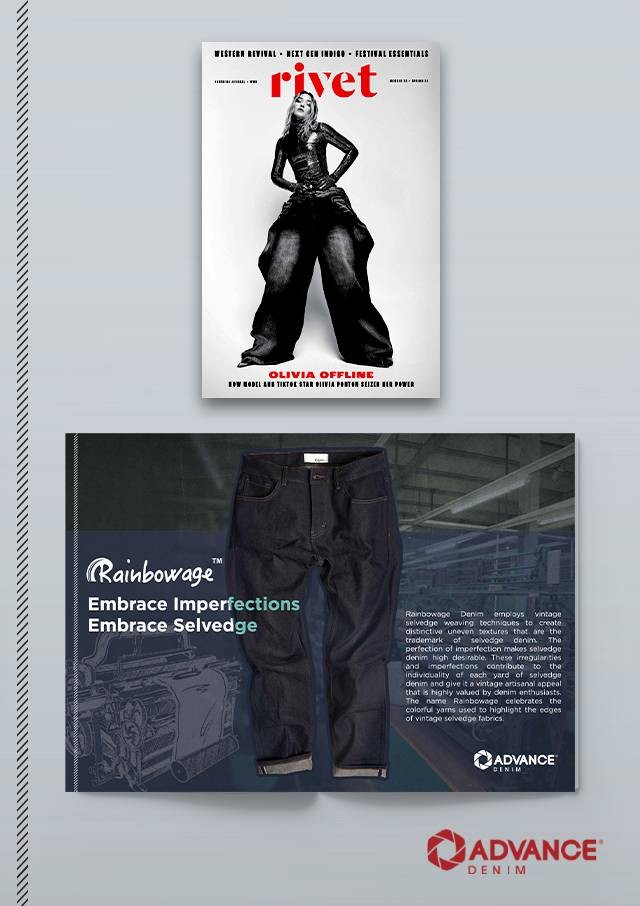
Embrace Imperfections Embrace Selvedge (Rivet Magazine)
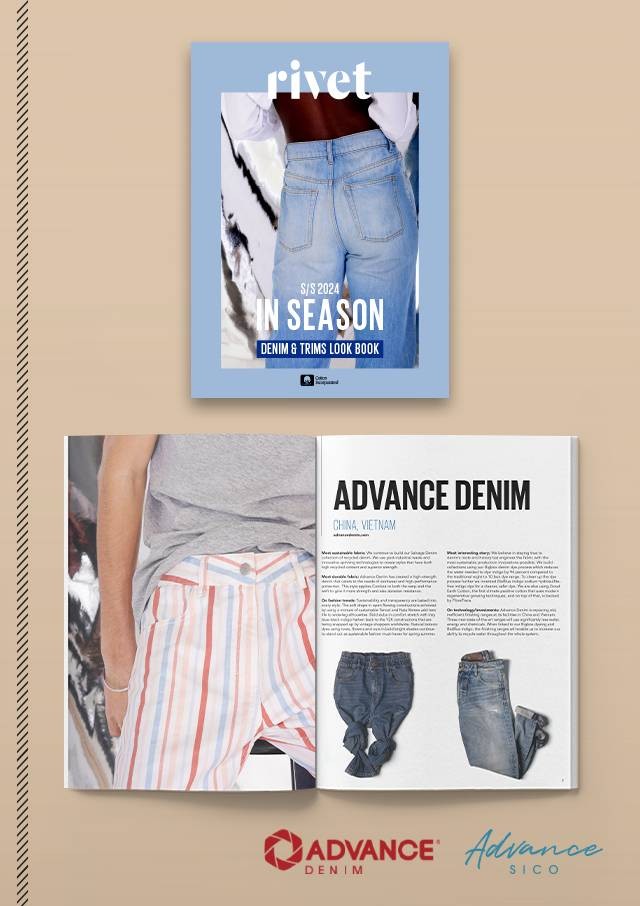
S/S 2024 IN SEASON DENIM LOOK BOOK (Rivet Magazine)
5 April 2024
5 April 2024
Explore
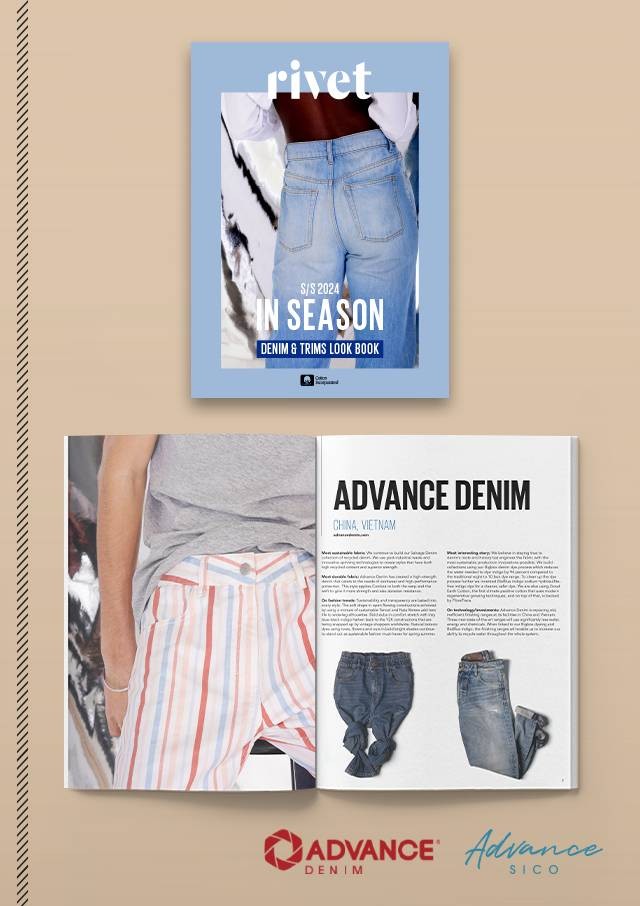
S/S 2024 IN SEASON DENIM LOOK BOOK (Rivet Magazine)
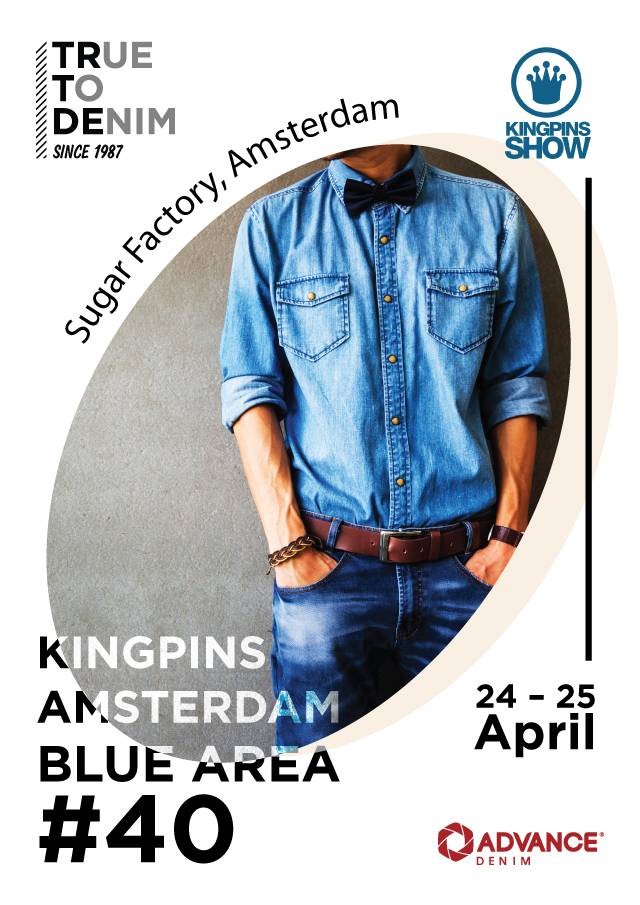
KINGPINS SHOW IN AMSTERDAM
17 April 2024
17 April 2024
Explore
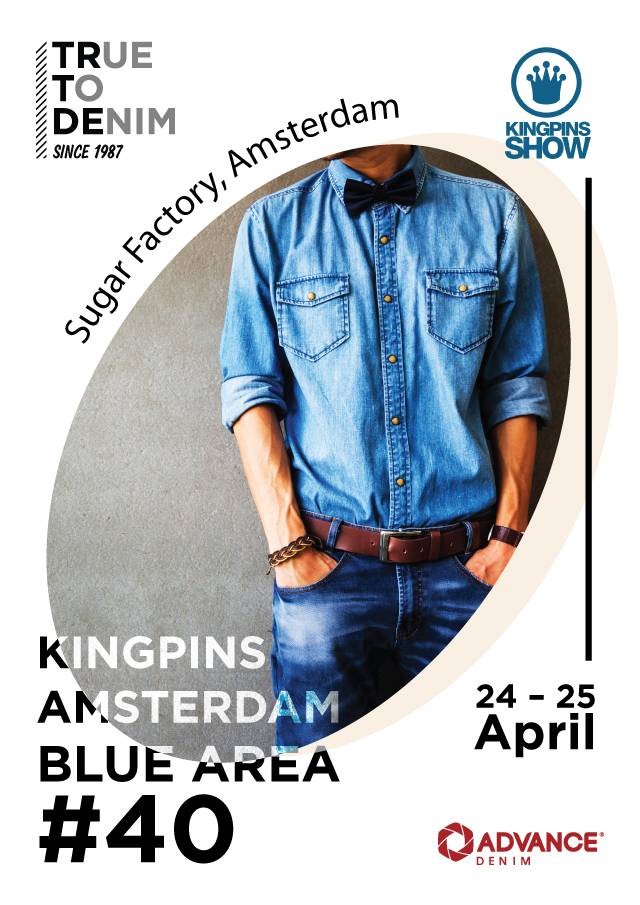
KINGPINS SHOW IN AMSTERDAM
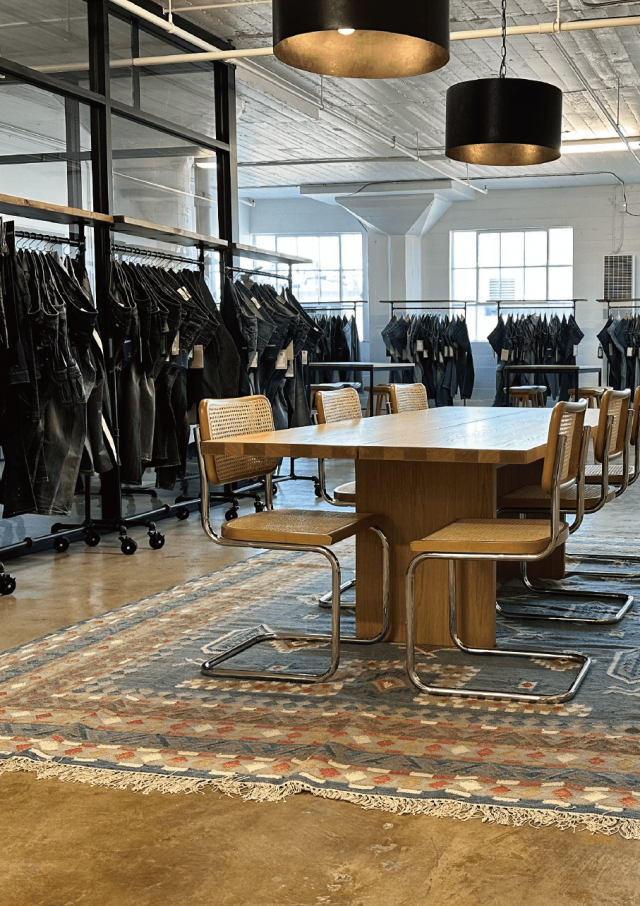
ADVANCE DENIM CONTINUES GLOBAL EXPANSION WITH NEW LOS ANGELES SHOWROOM (Rivet Magazine)
21 March 2024
21 March 2024
Explore
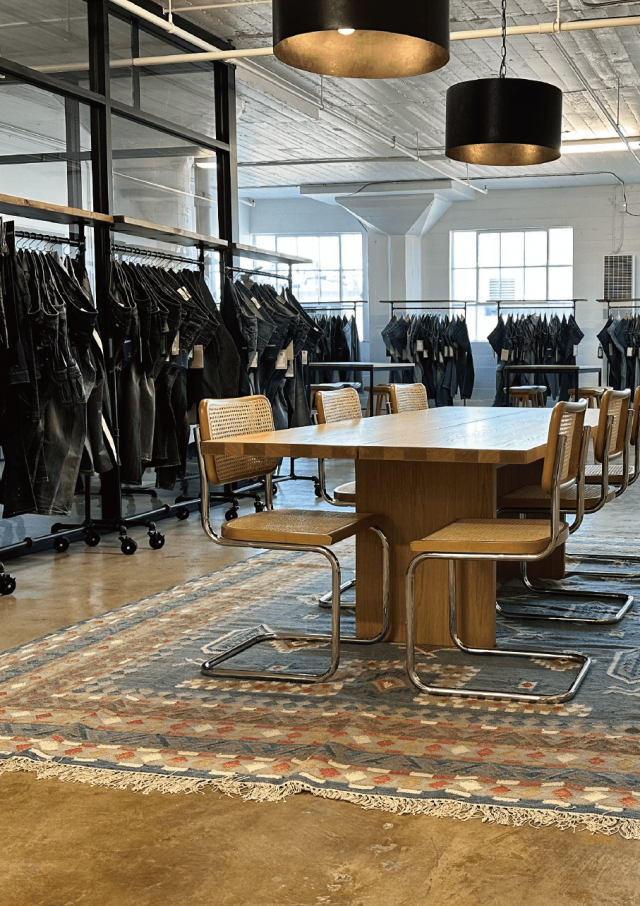
ADVANCE DENIM CONTINUES GLOBAL EXPANSION WITH NEW LOS ANGELES SHOWROOM (Rivet Magazine)
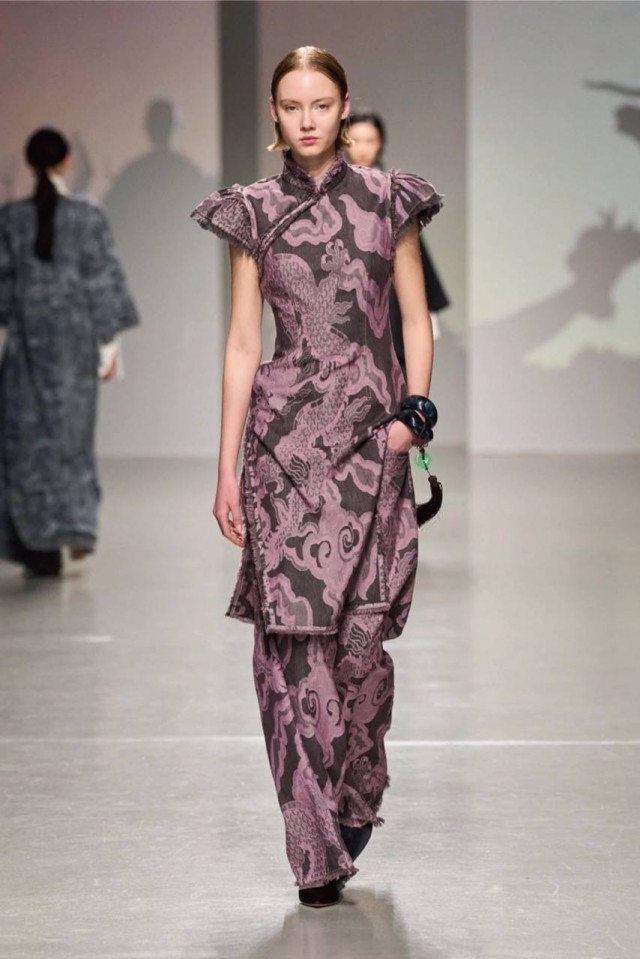
Advance Denim X Vivienne Tam
14 March 2024
14 March 2024
Explore
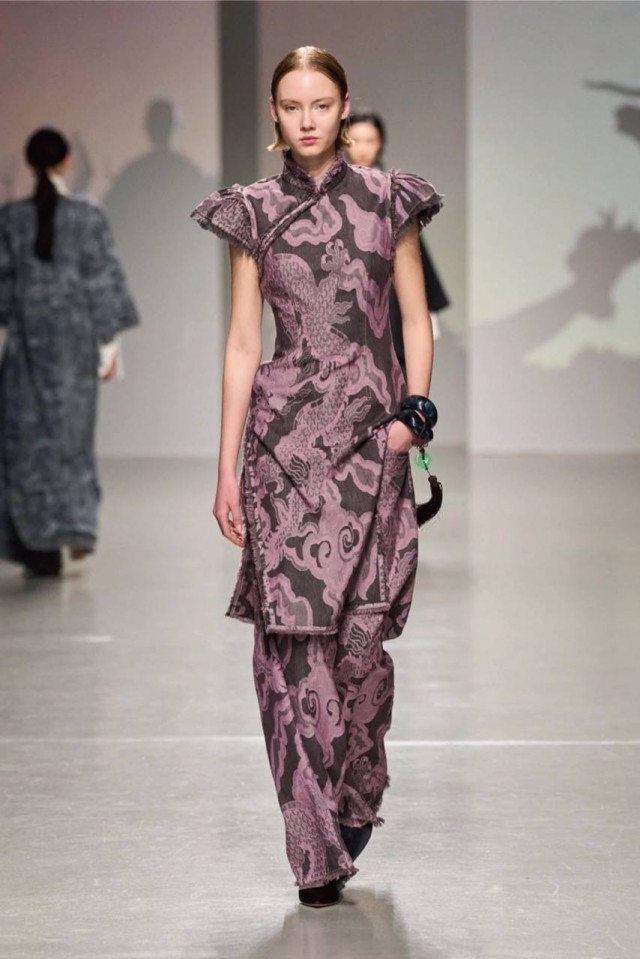
Advance Denim X Vivienne Tam
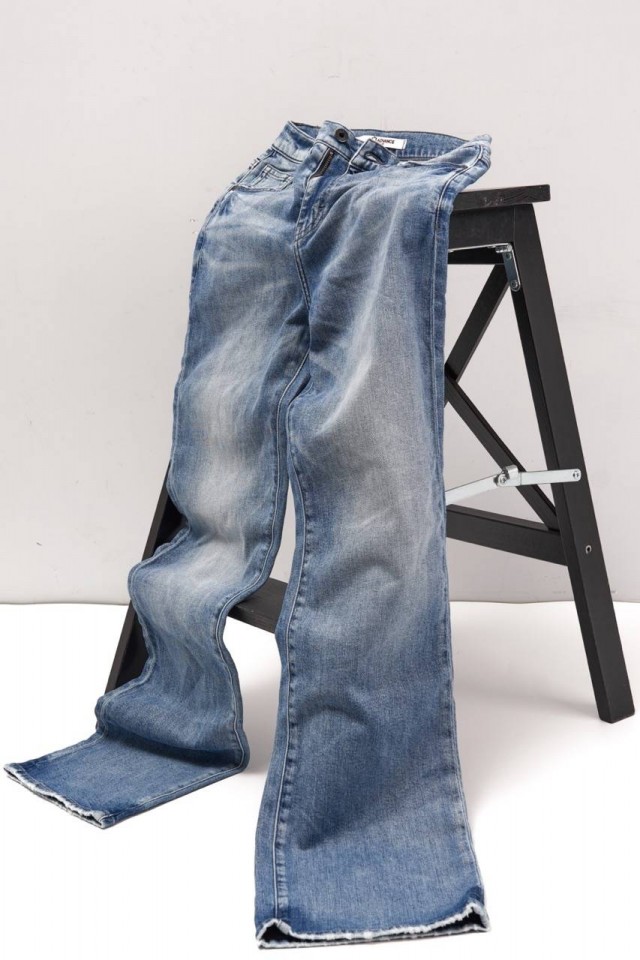
ADVANCE DENIM’S MATTE TENCEL™ COLLECTION
1 March 2024
1 March 2024
Explore
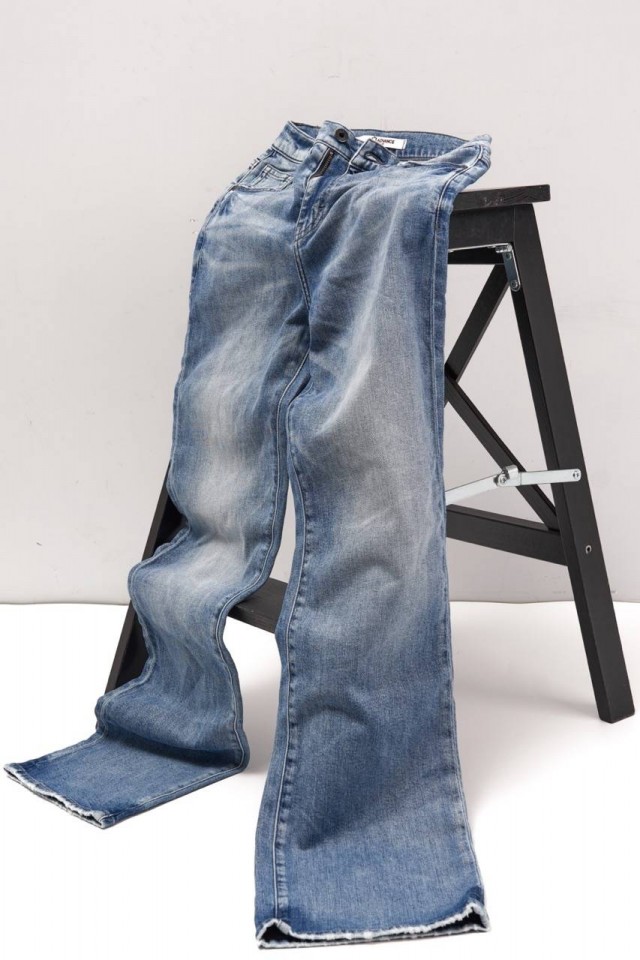
ADVANCE DENIM’S MATTE TENCEL™ COLLECTION
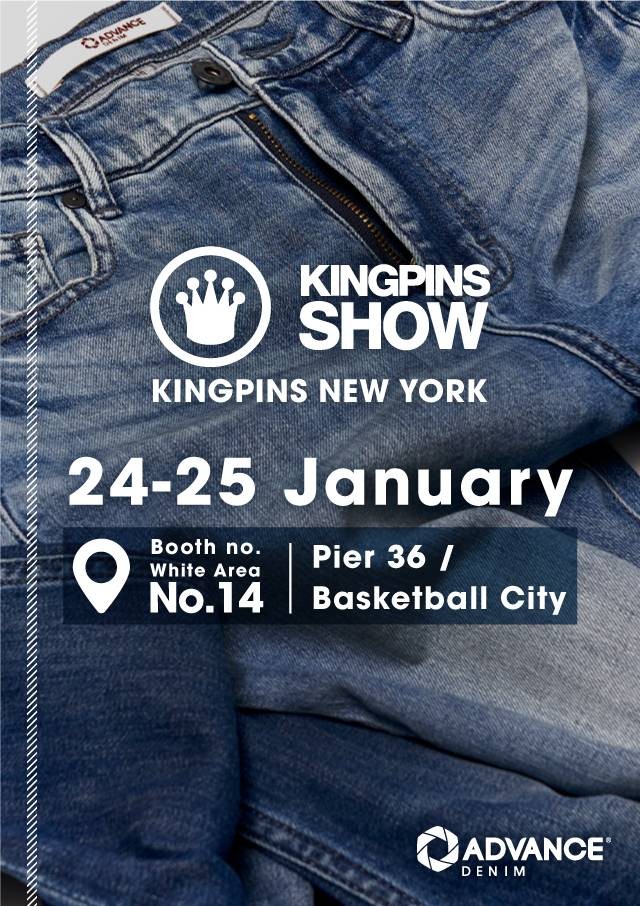
KINGPINS SHOW IN NEW YORK
24 January 2024
24 January 2024
Explore
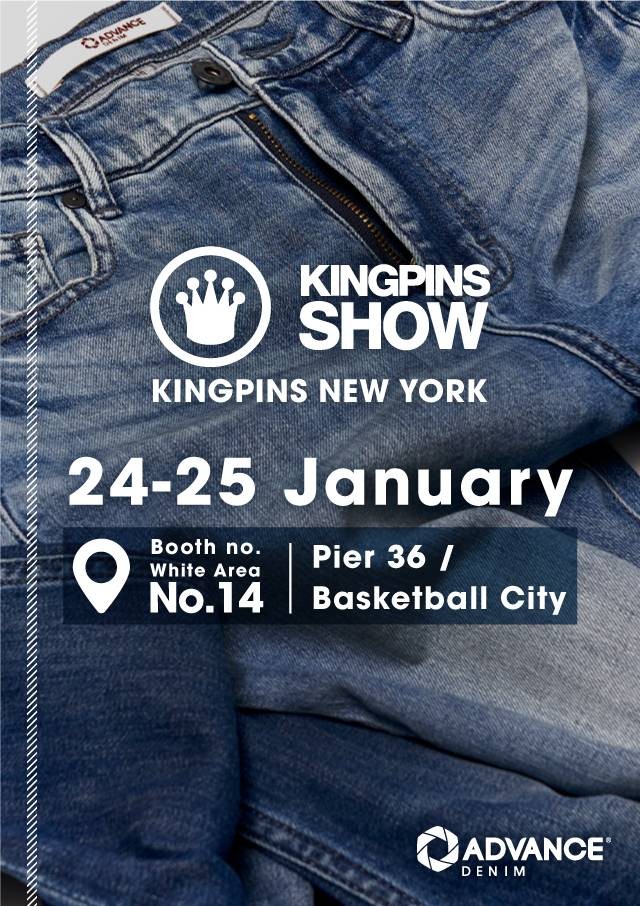
KINGPINS SHOW IN NEW YORK
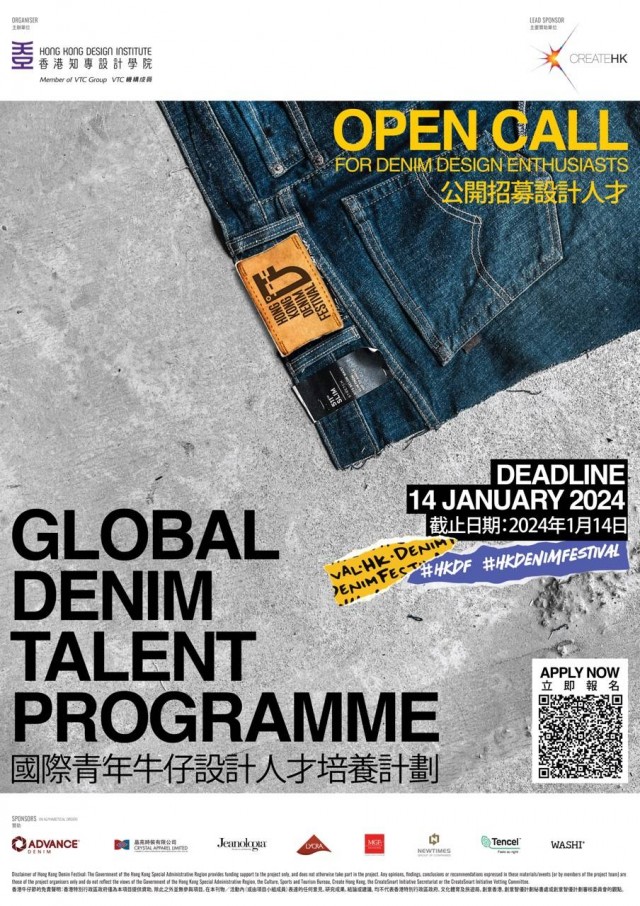
Global Denim Talent Programme
19 December 2023
19 December 2023
Explore
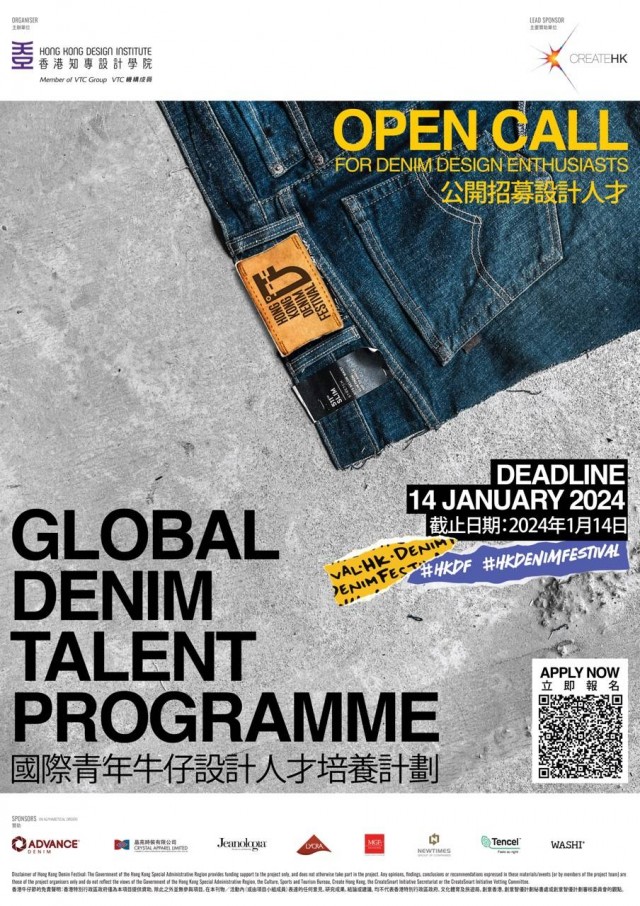
Global Denim Talent Programme
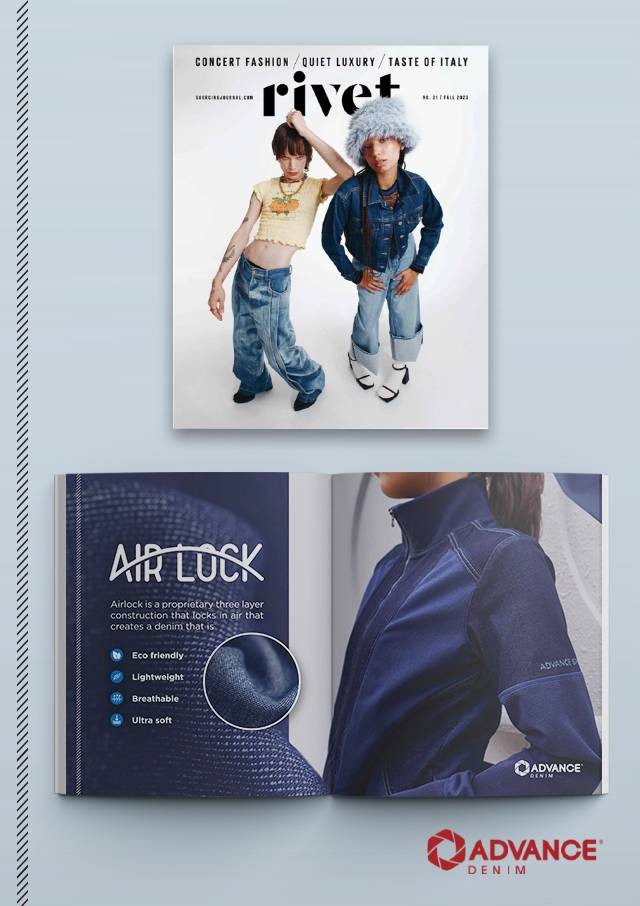
ADVANCE DENIM - AIR LOCK COLLECTION
18 December 2023
18 December 2023
Explore
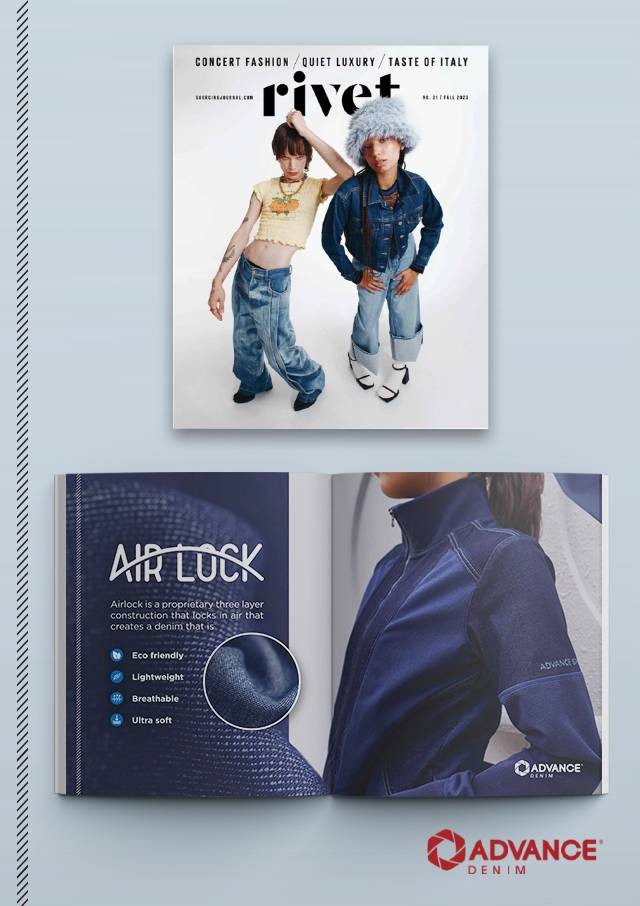
ADVANCE DENIM - AIR LOCK COLLECTION
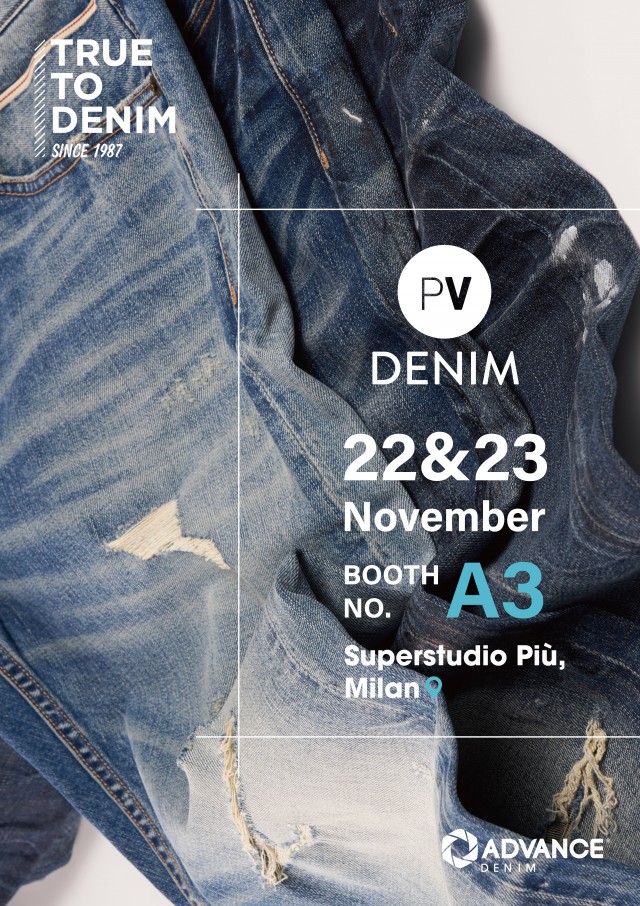
Denim Première Vision Show in Milan
22 November 2023
22 November 2023
Explore
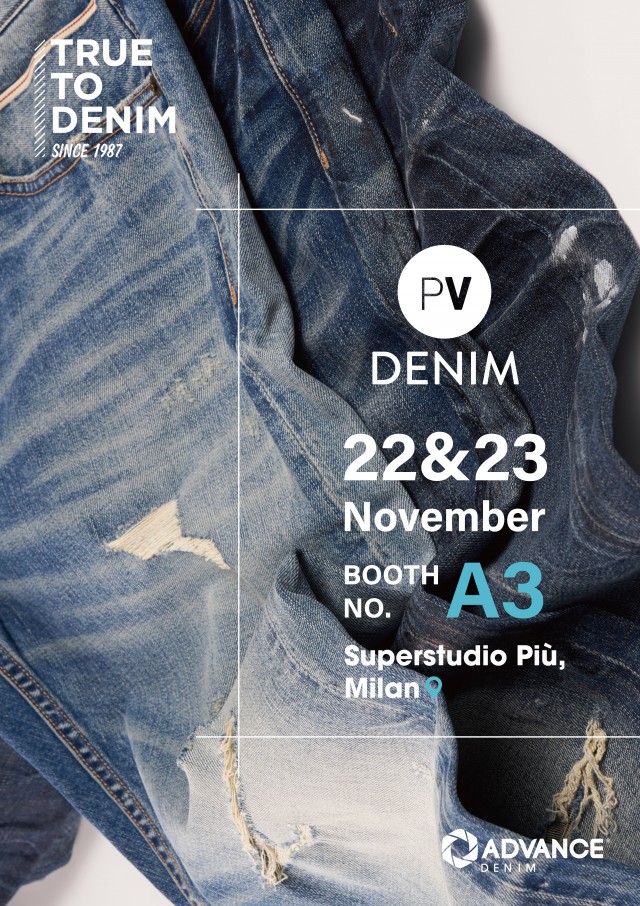
Denim Première Vision Show in Milan
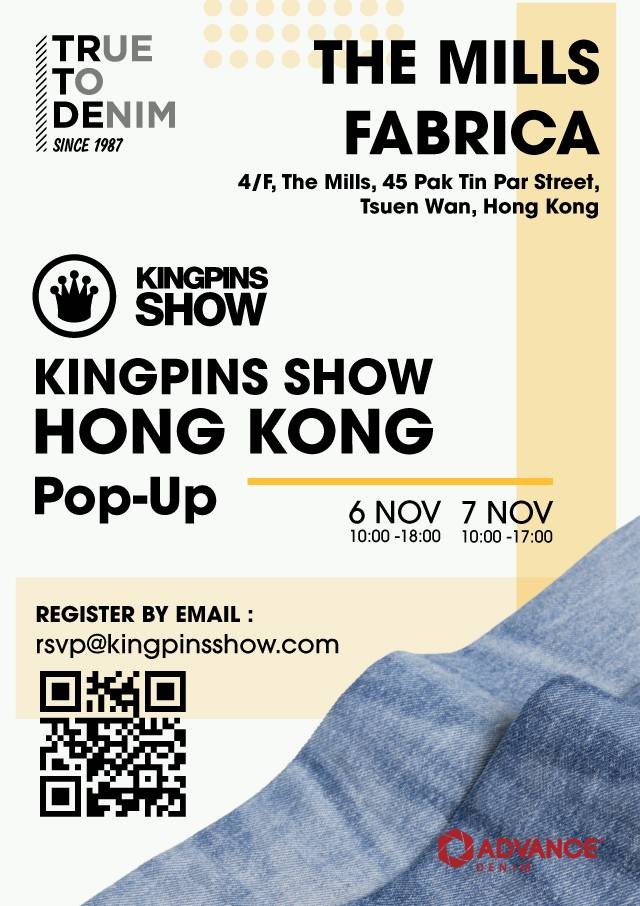
KINGPINS SHOW POP-UP IN HONG KONG
1 November 2023
1 November 2023
Explore
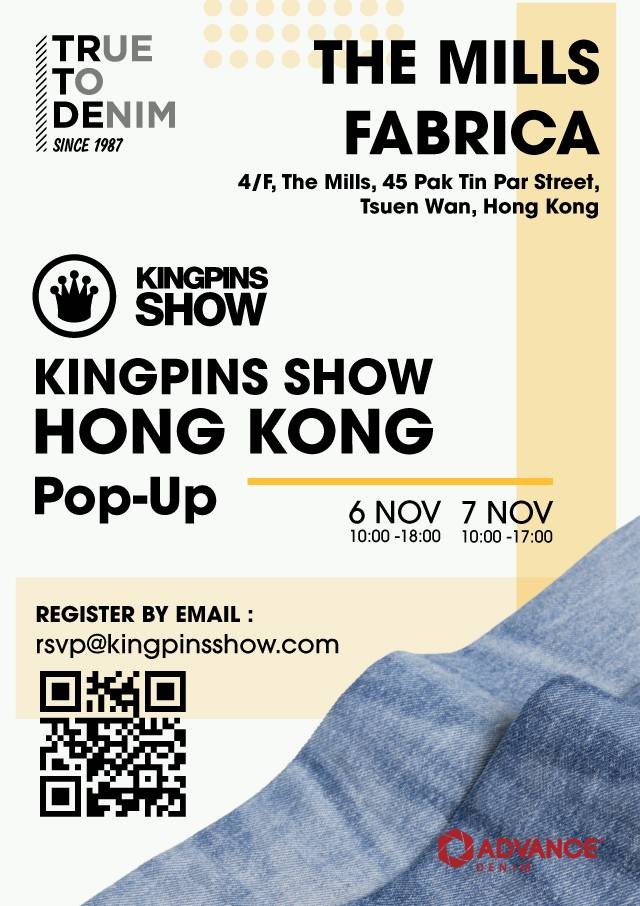
KINGPINS SHOW POP-UP IN HONG KONG
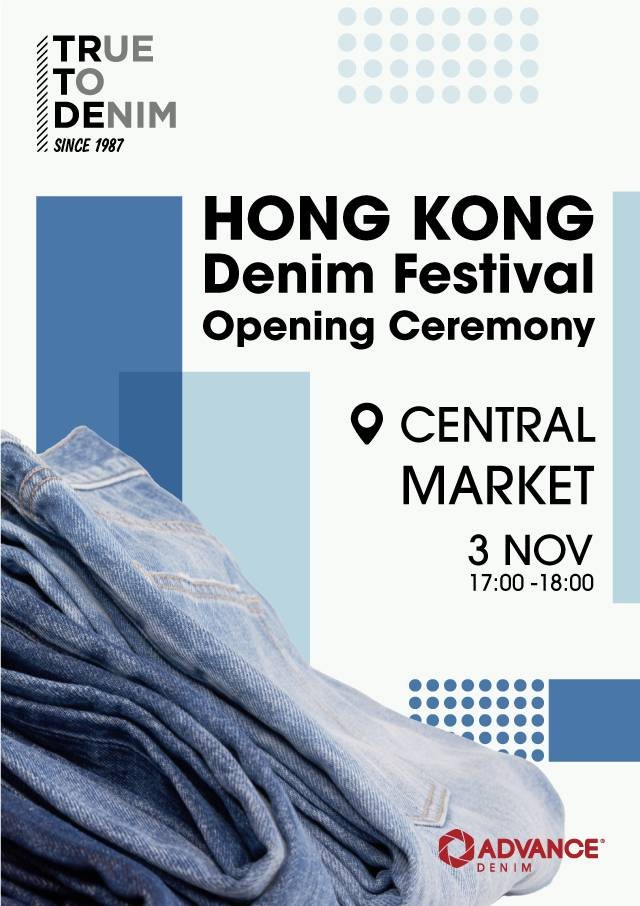
Hong Kong Denim Festival Opening Ceremony
1 November 2023
1 November 2023
Explore
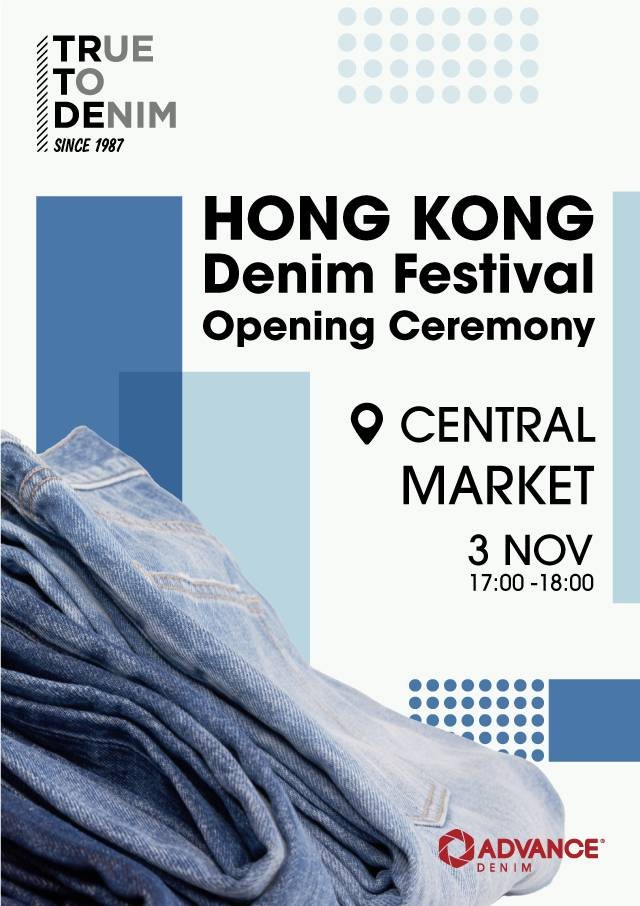
Hong Kong Denim Festival Opening Ceremony
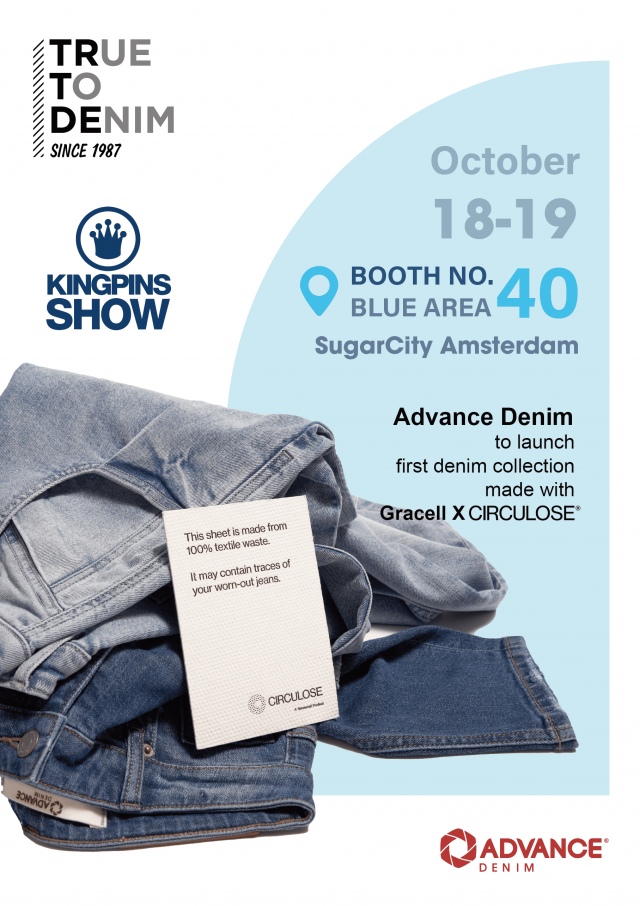
KINGPINS SHOW IN AMSTERDAM
12 October 2023
12 October 2023
Explore
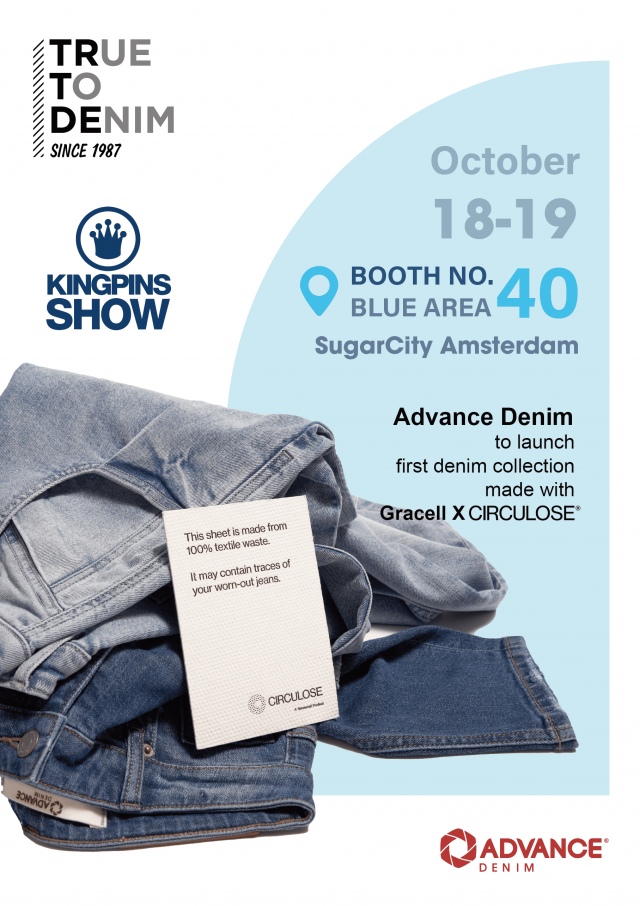
KINGPINS SHOW IN AMSTERDAM
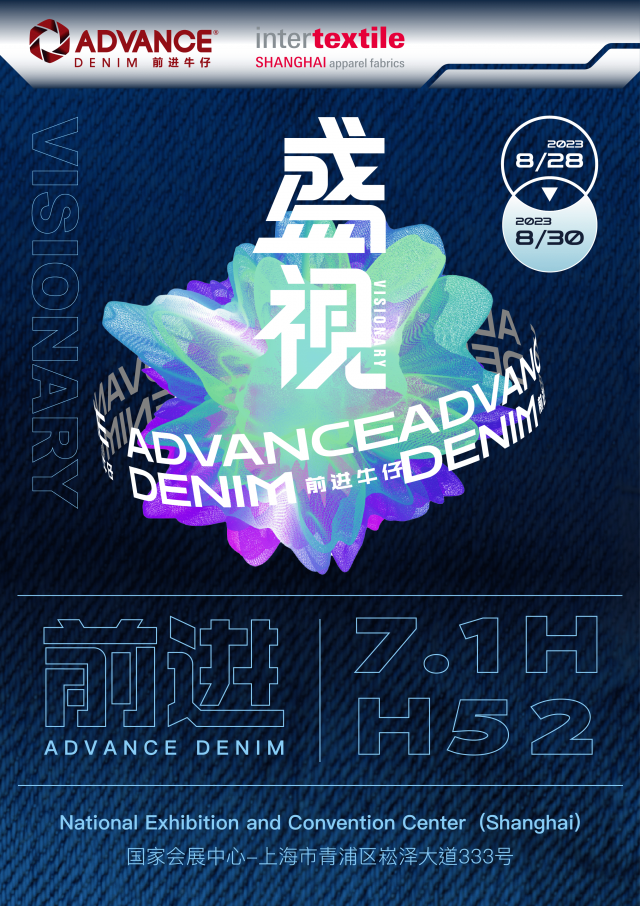
Intertextile Shanghai Apparel Fabrics
28 August 2023
28 August 2023
Explore
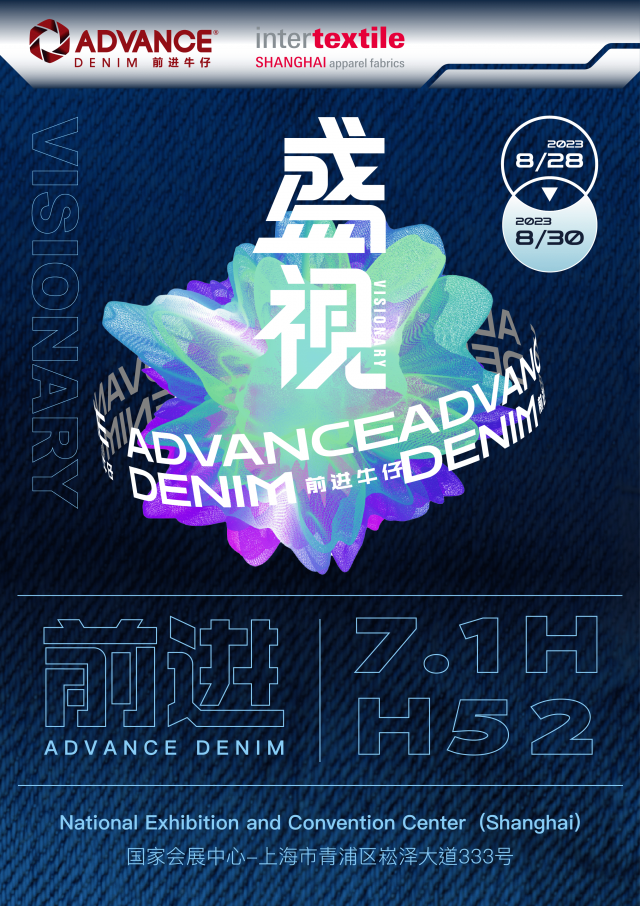
Intertextile Shanghai Apparel Fabrics
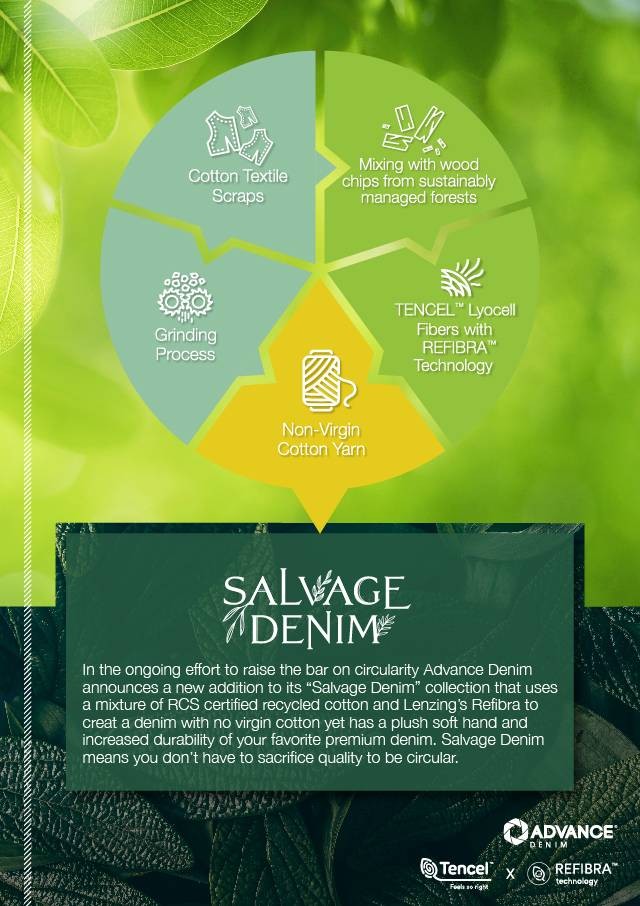
Salvage Denim (Non Virgin Cotton Yarn)
15 August 2023
15 August 2023
Explore
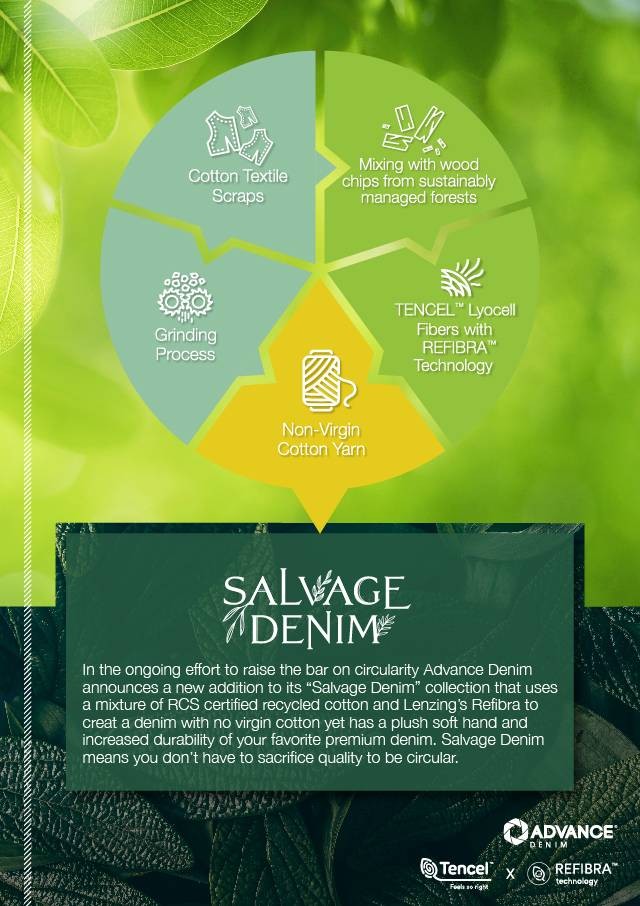
Salvage Denim (Non Virgin Cotton Yarn)
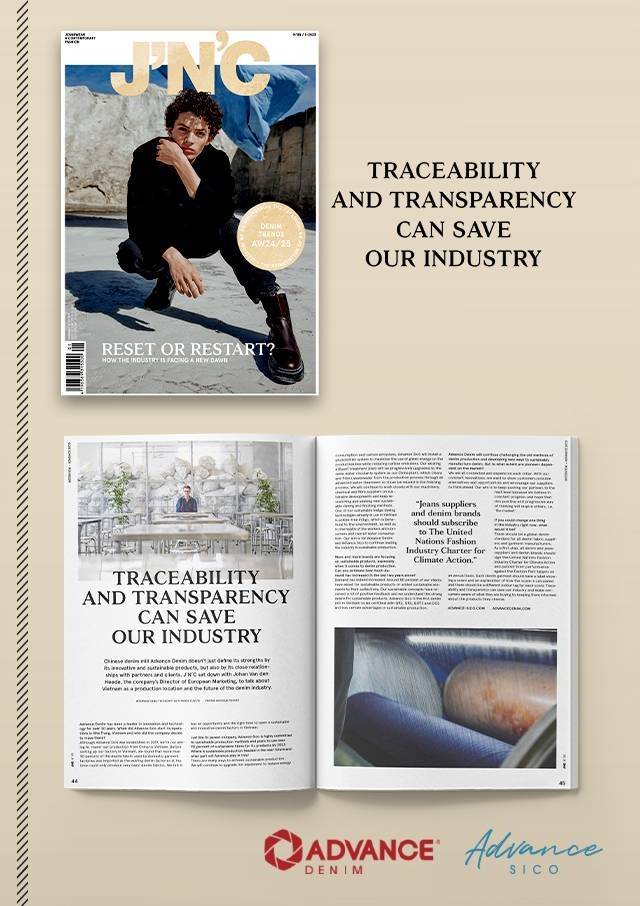
Traceability and Transparency Can Save Our Industry (J'N'C Magazine)
25 July 2023
25 July 2023
Explore
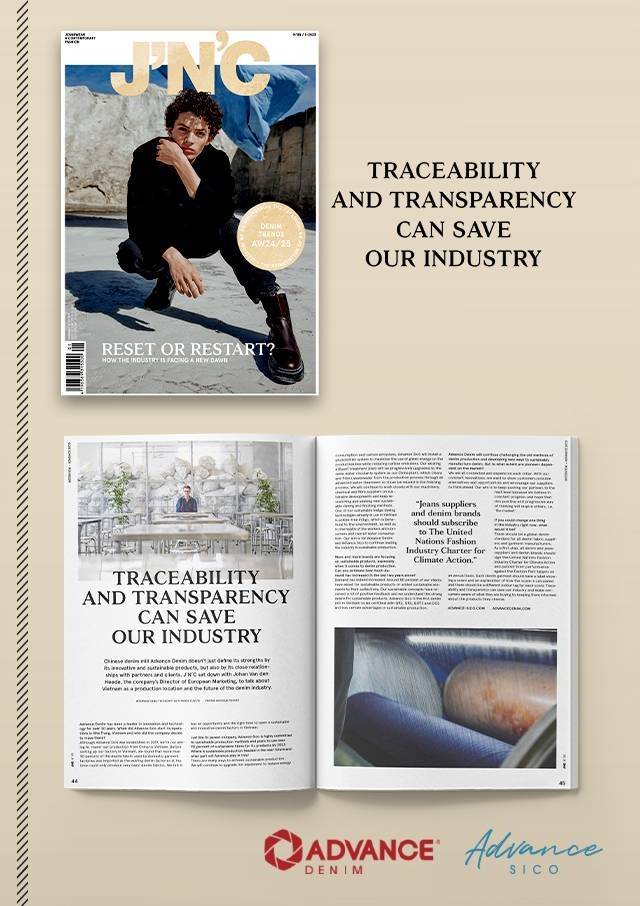
Traceability and Transparency Can Save Our Industry (J'N'C Magazine)
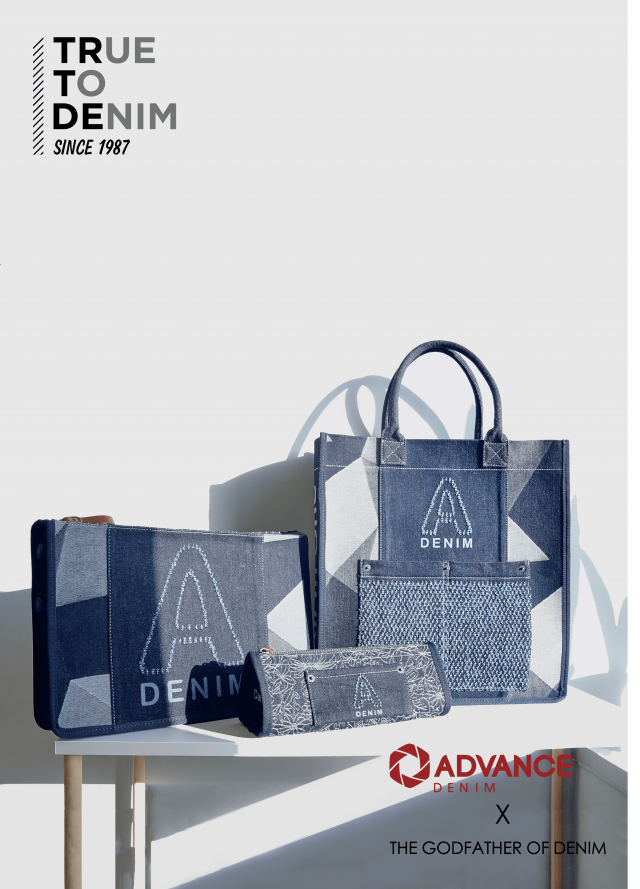
Advance Denim Collaborate with the Godfather of Denim to Create an Exclusive Collection of Denim Bags
19 July 2023
19 July 2023
Explore
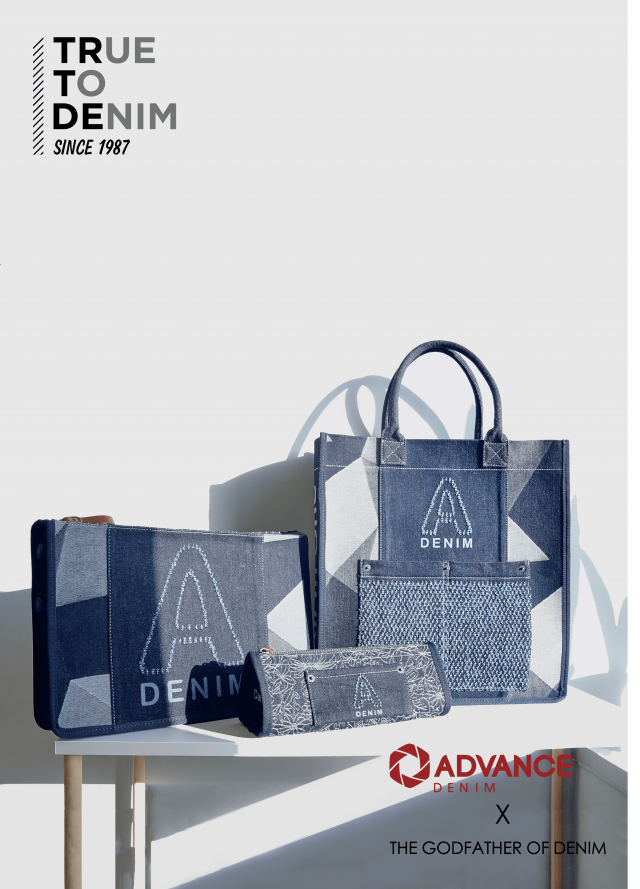
Advance Denim Collaborate with the Godfather of Denim to Create an Exclusive Collection of Denim Bags
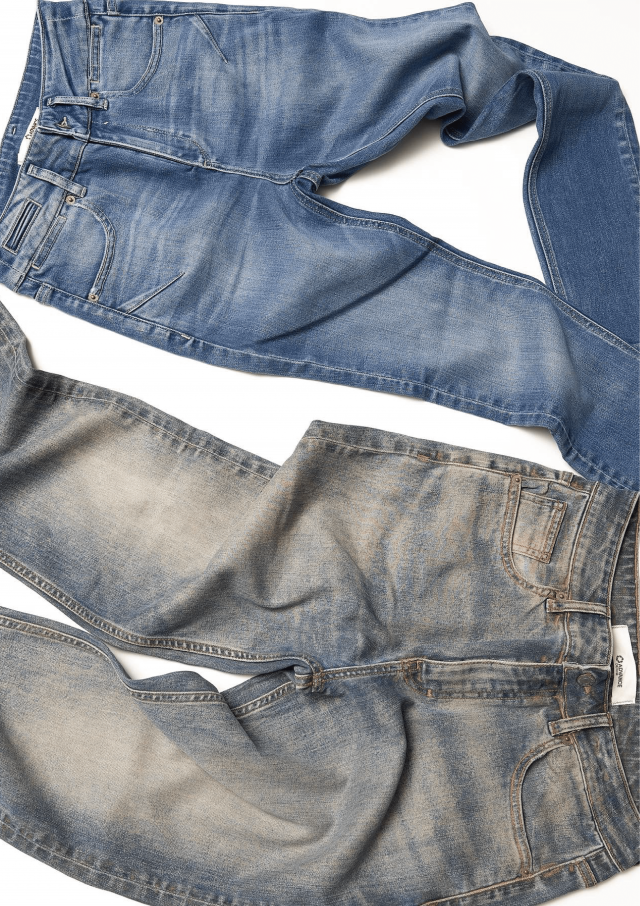
Supply Chain Partners to Add Character to Zero-Cotton Denim Fabrics
13 July 2023
13 July 2023
Explore
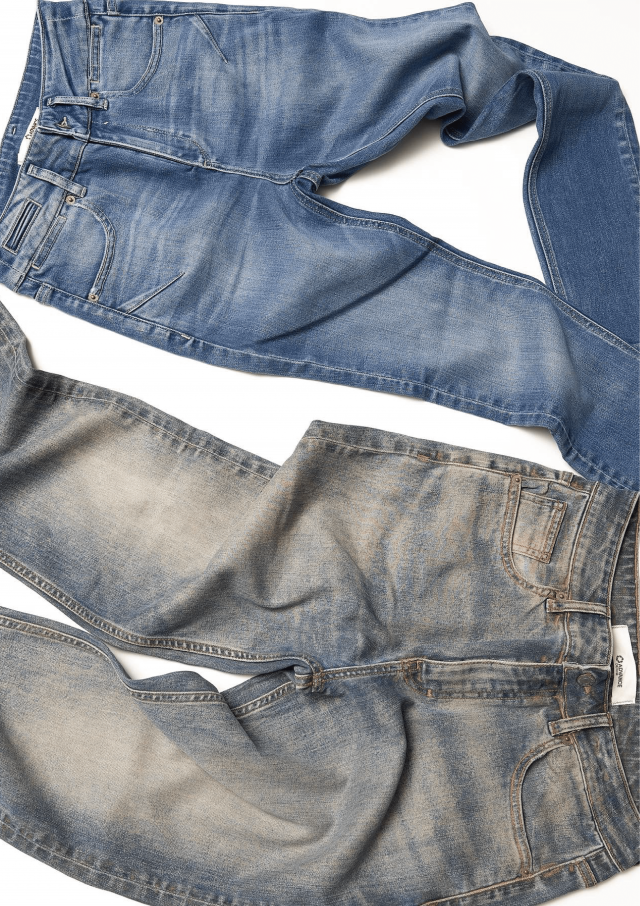
Supply Chain Partners to Add Character to Zero-Cotton Denim Fabrics
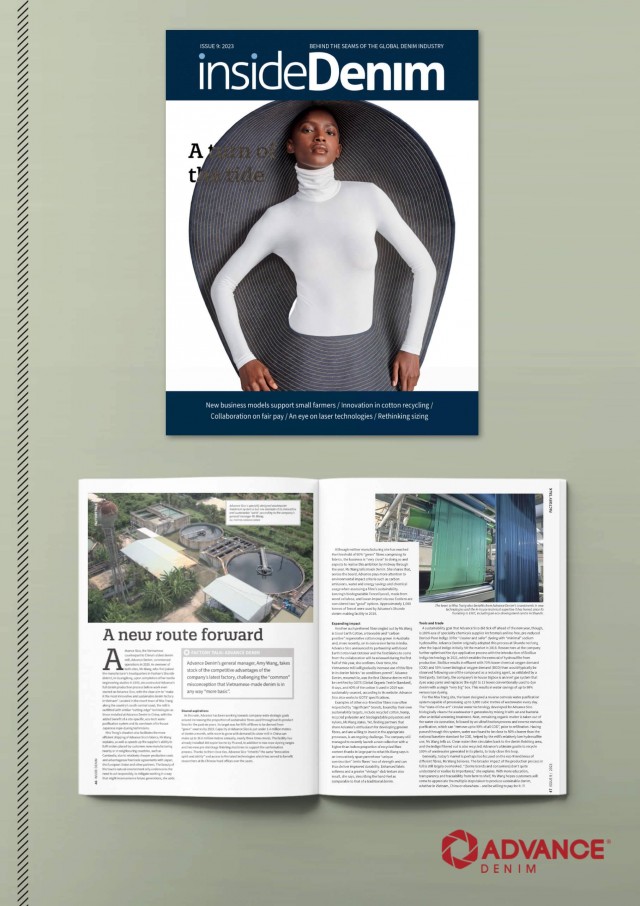
A new route forward (Inside Denim Magazine)
5 July 2023
5 July 2023
Explore
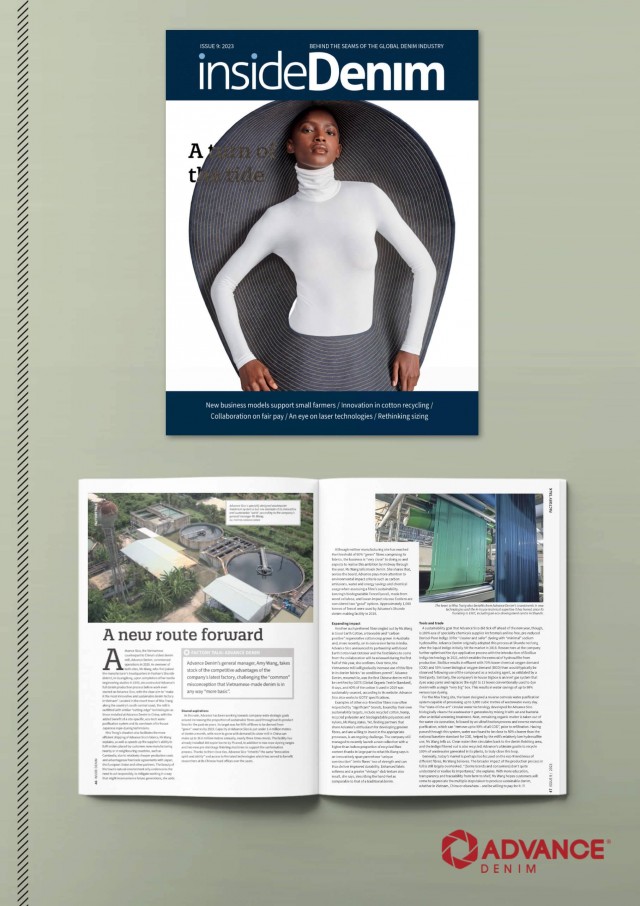
A new route forward (Inside Denim Magazine)
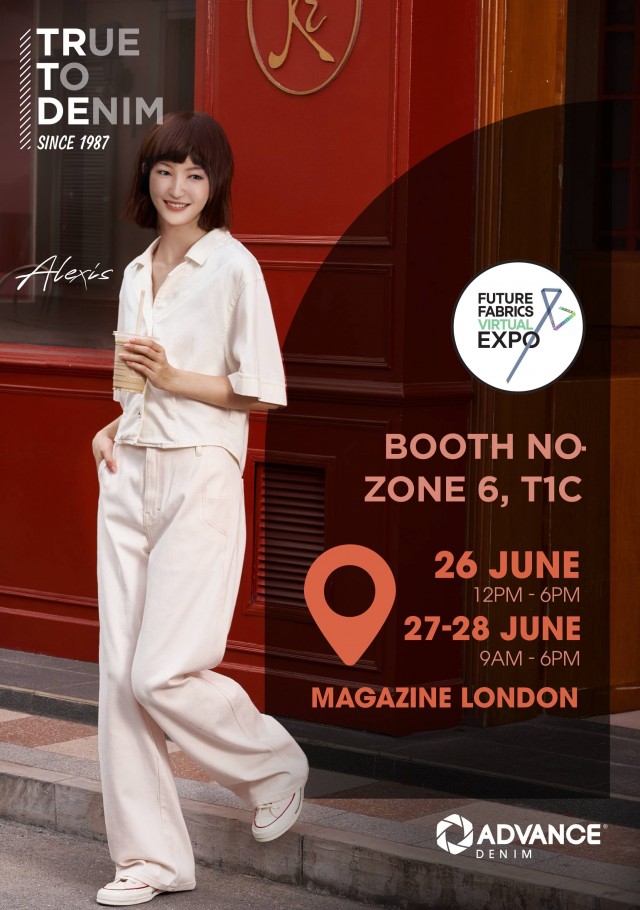
Future Fabrics Expo in London
26-28 June 2023
26-28 June 2023
Explore
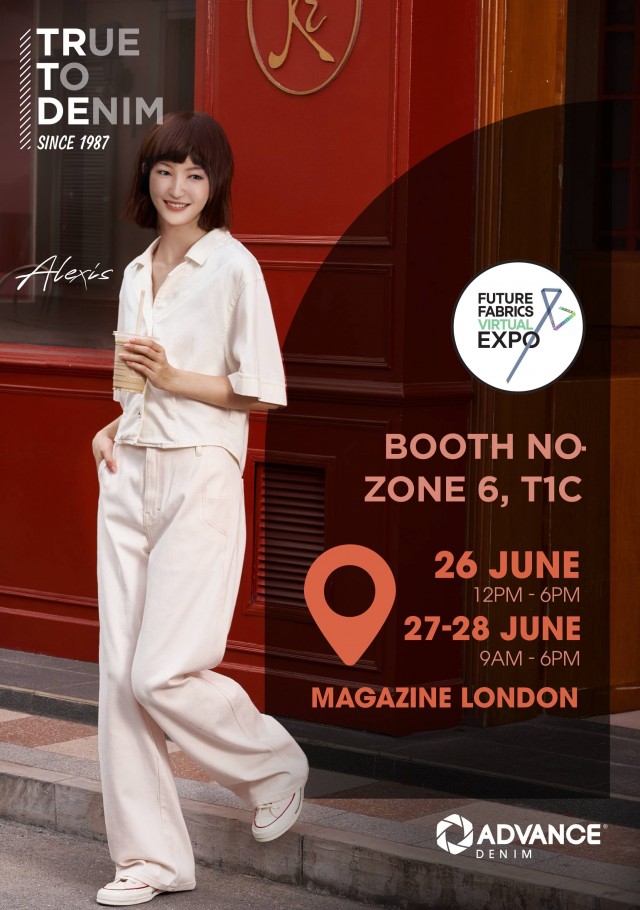
Future Fabrics Expo in London
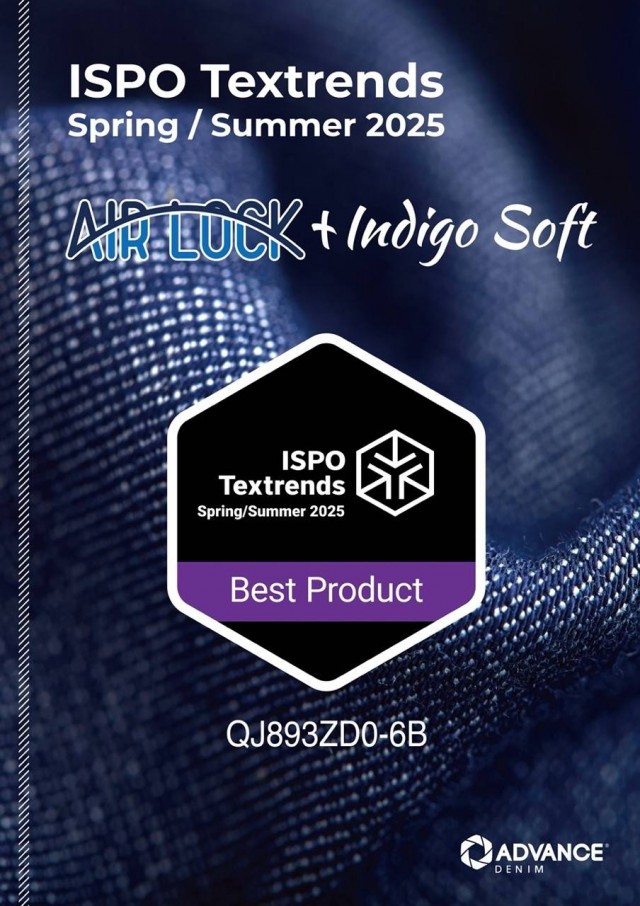
Best Product of The ISPO TEXTRENDS Spring and Summer 2025
20 June 2023
20 June 2023
Explore
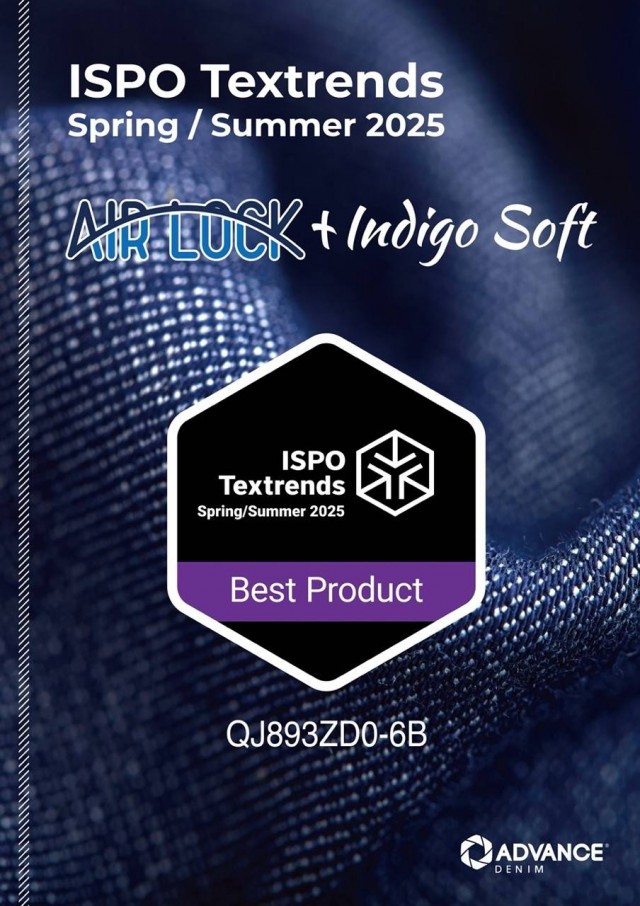
Best Product of The ISPO TEXTRENDS Spring and Summer 2025
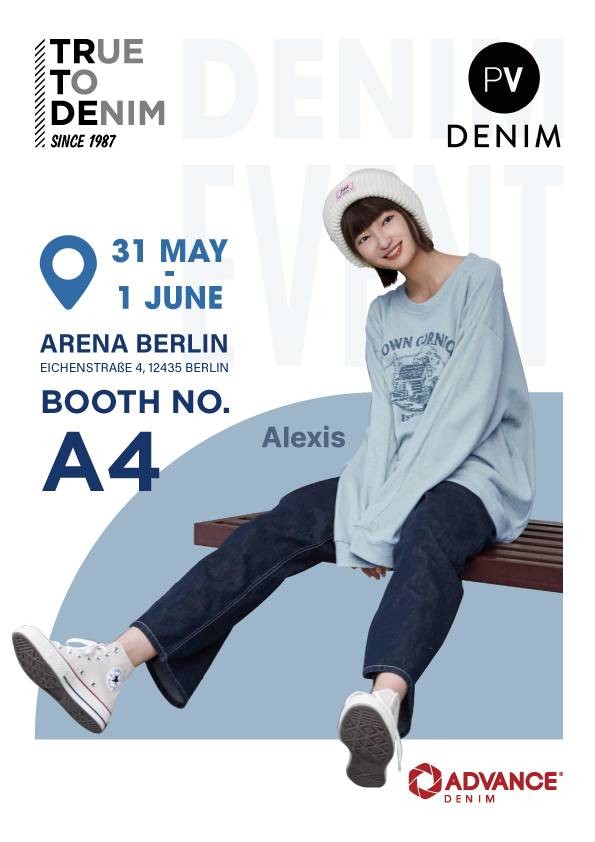
DENIM PREMIÈRE VISION SHOW IN BERLIN
28 May 2023
28 May 2023
Explore
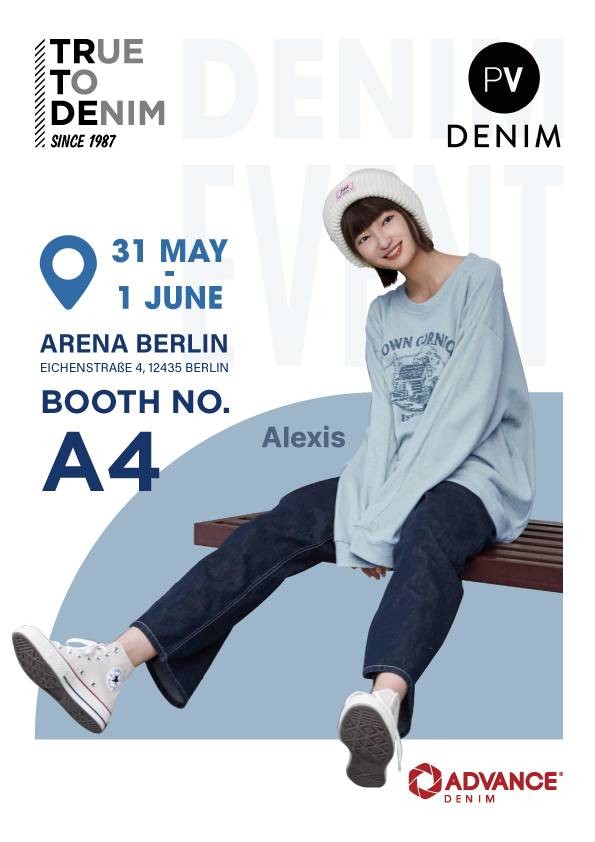
DENIM PREMIÈRE VISION SHOW IN BERLIN
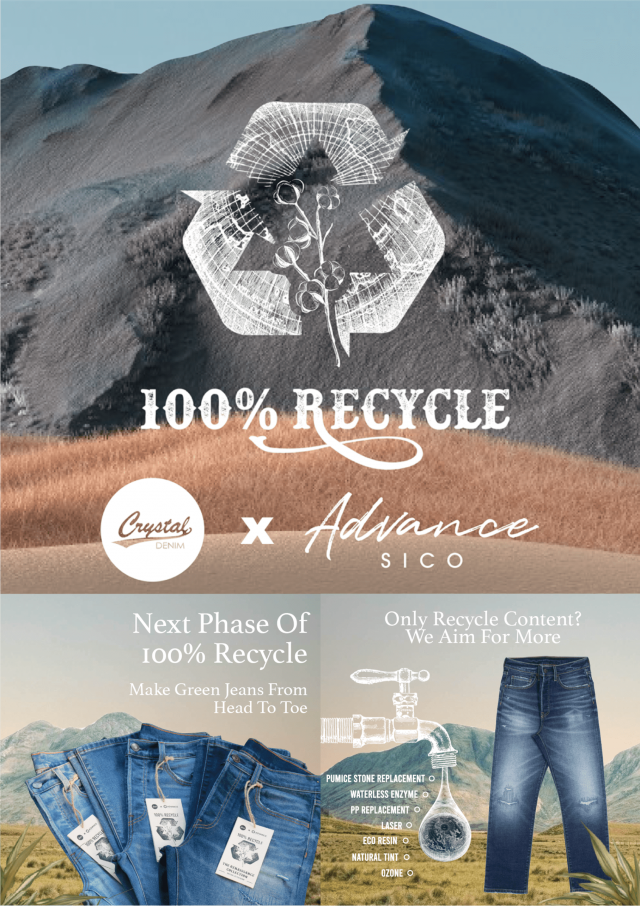
Advance Sico × Crystal Group
8 May 2023
8 May 2023
Explore
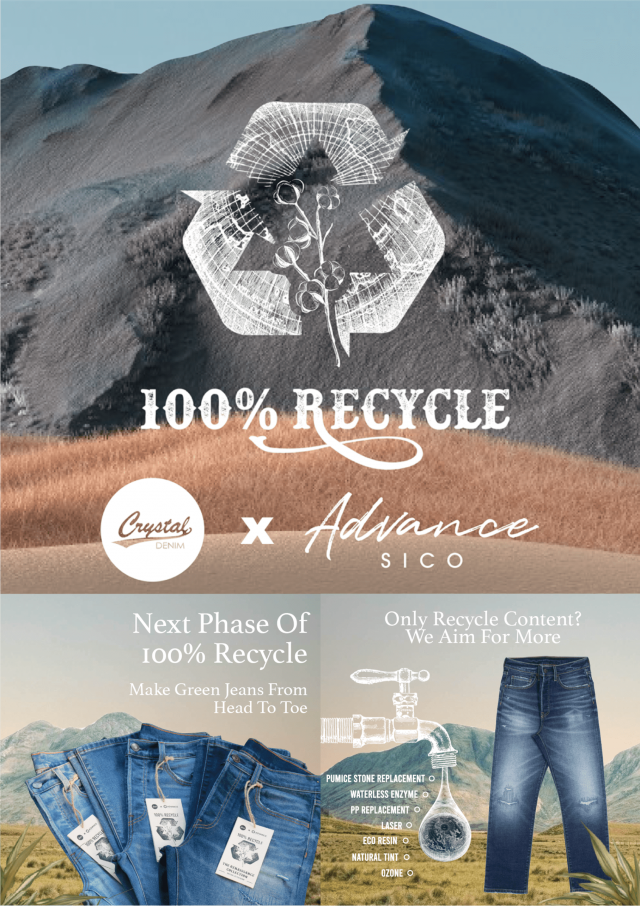
Advance Sico × Crystal Group
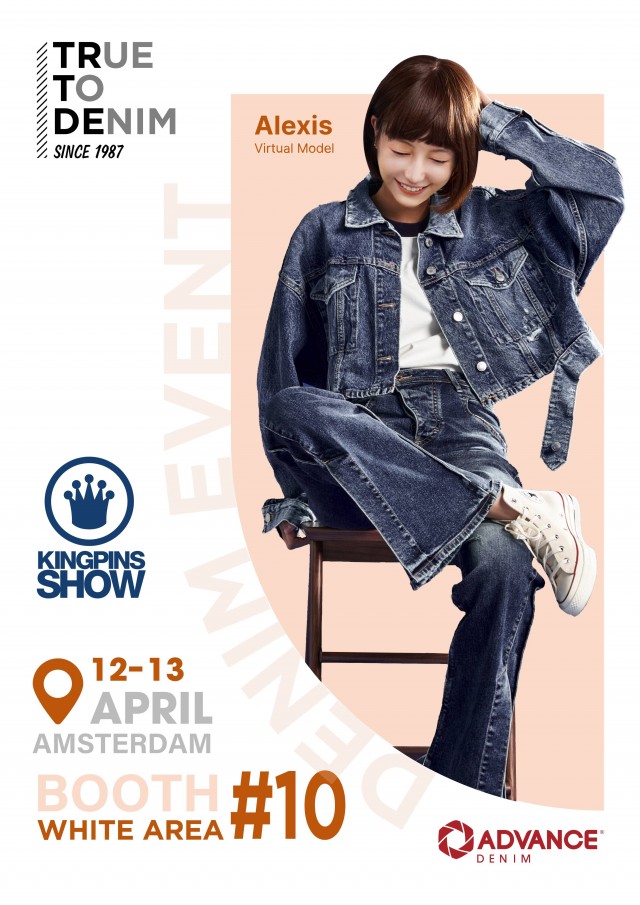
KINGPINS SHOW IN AMSTERDAM
12-13 April 2023
12-13 April 2023
Explore
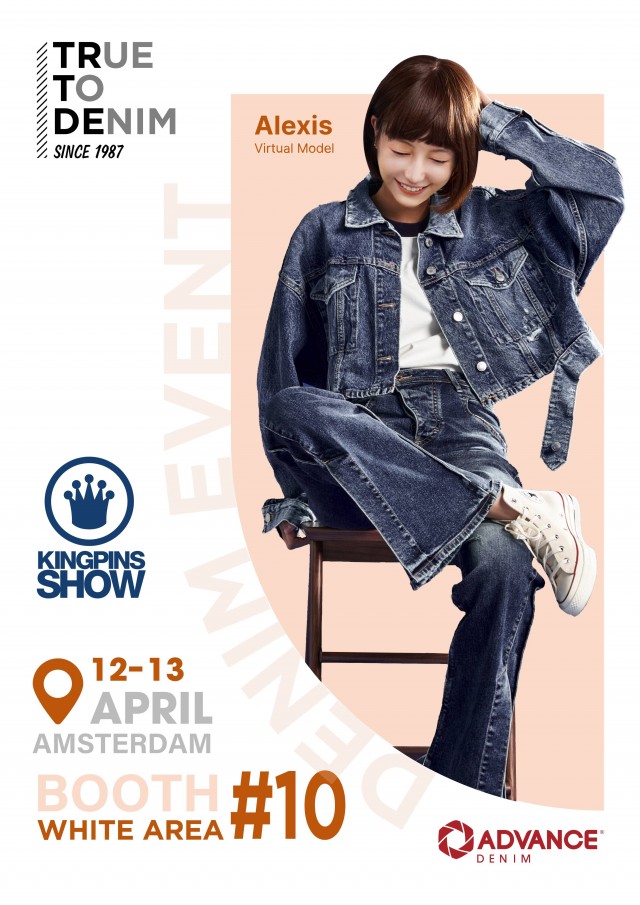
KINGPINS SHOW IN AMSTERDAM
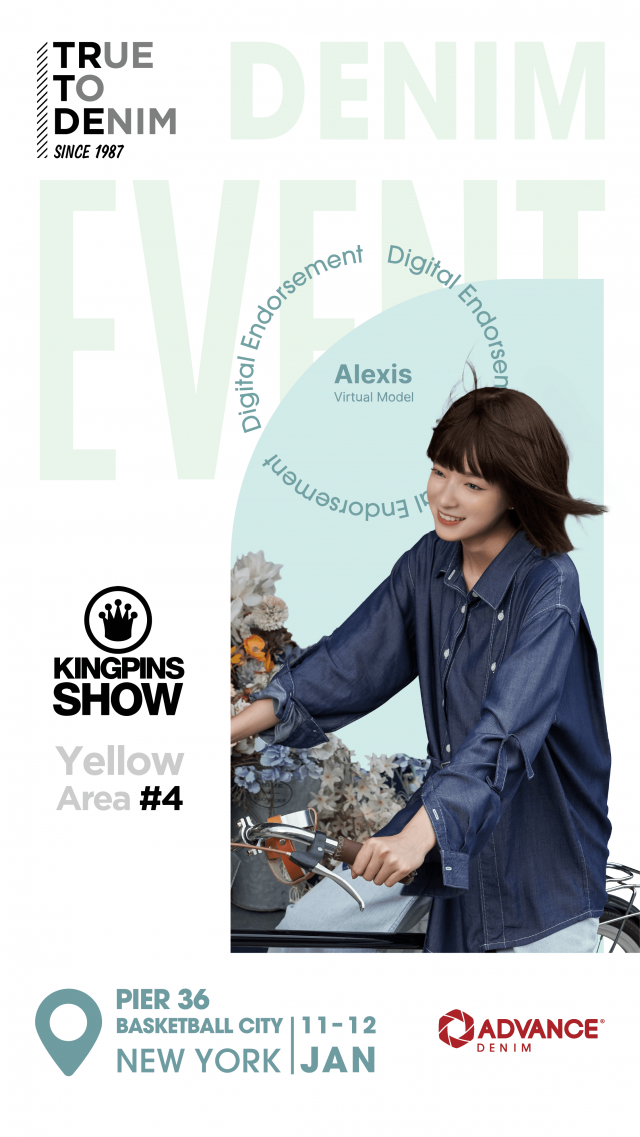
KINGPINS SHOW IN NEW YORK
11-12 January 2023
11-12 January 2023
Explore
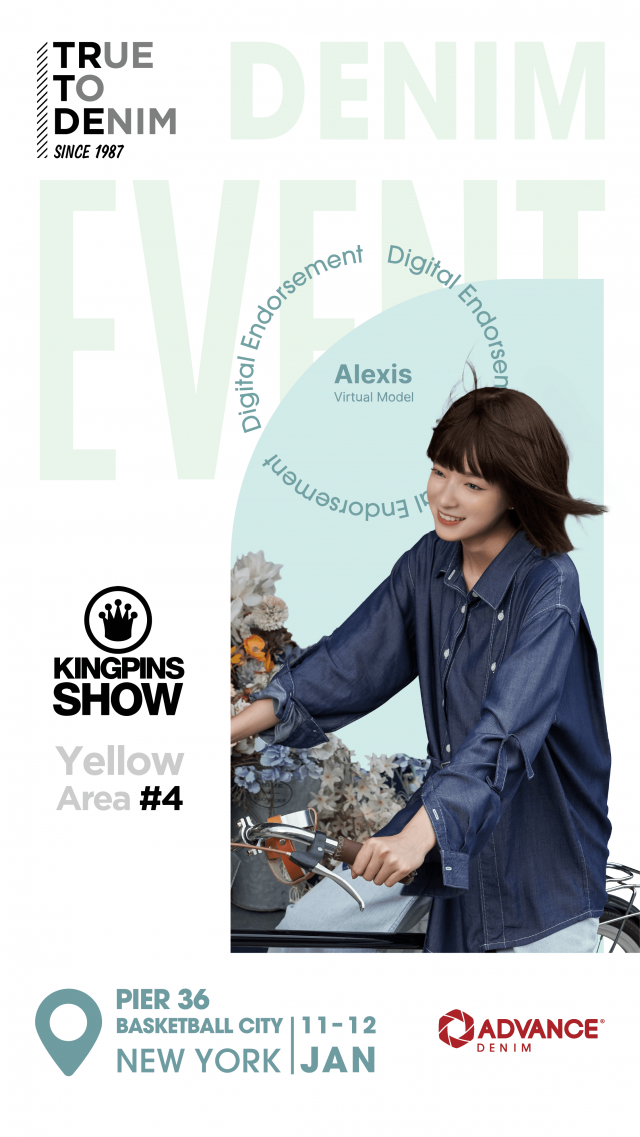
KINGPINS SHOW IN NEW YORK
DENIM PREMIÈRE VISION SHOW IN MILAN
22 Nov 2022
22 Nov 2022
Explore
DENIM PREMIÈRE VISION SHOW IN MILAN
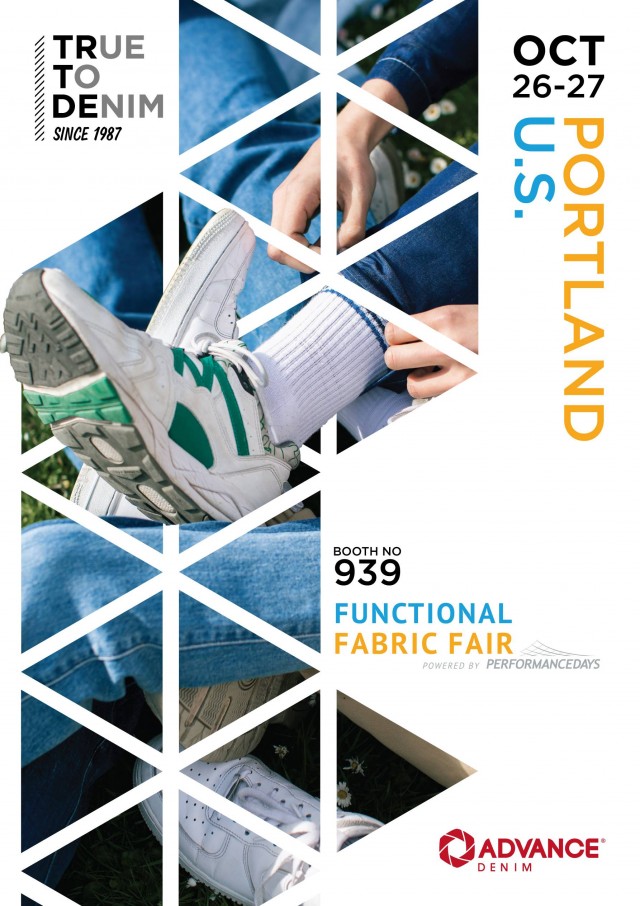
Functional Fabric Fair in Portland U.S
25 Oct 2022
25 Oct 2022
Explore
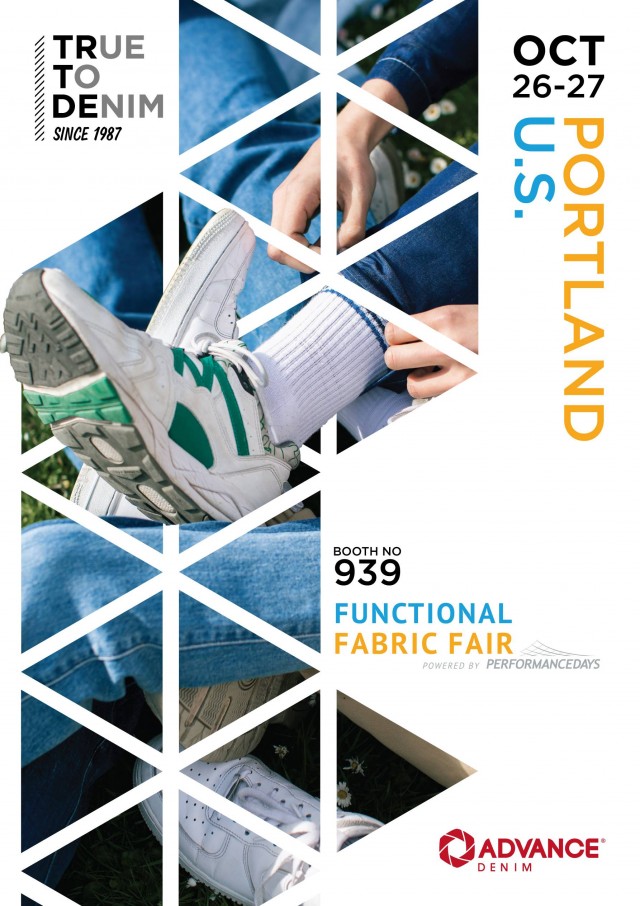
Functional Fabric Fair in Portland U.S
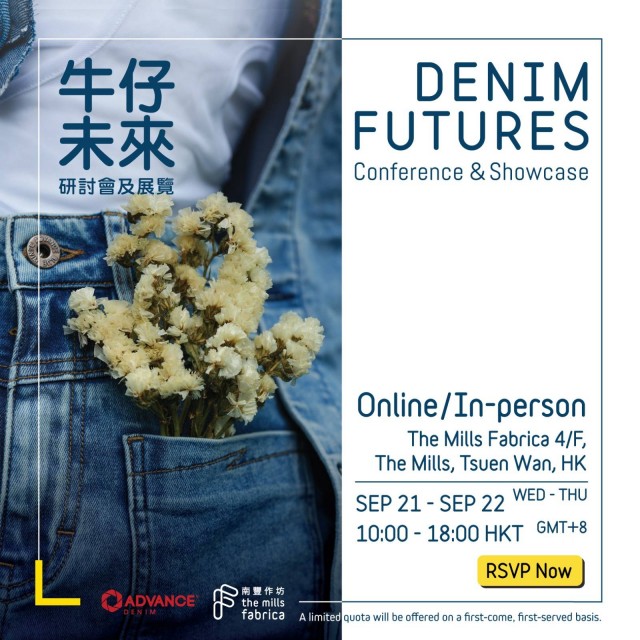
Denim Futures Conference & Showcase
20 Sep 2022
20 Sep 2022
Explore
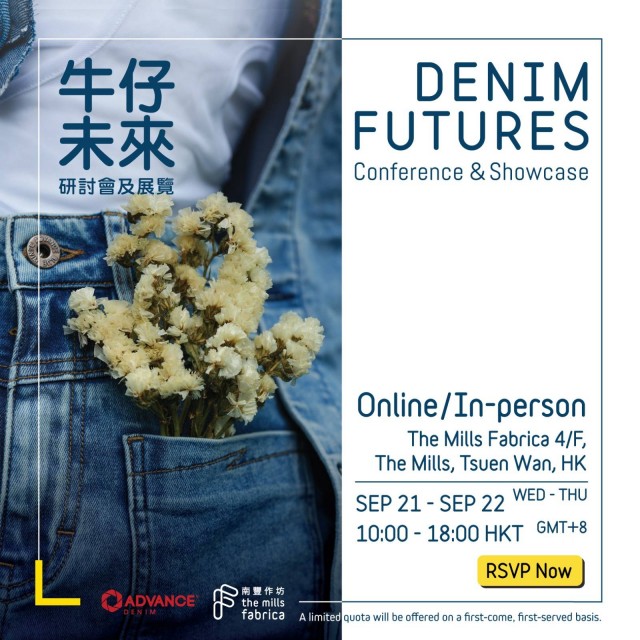
Denim Futures Conference & Showcase

Blue Zone Denim Trade Show in Munich Germany
30 August 2022
30 August 2022
Explore

Blue Zone Denim Trade Show in Munich Germany
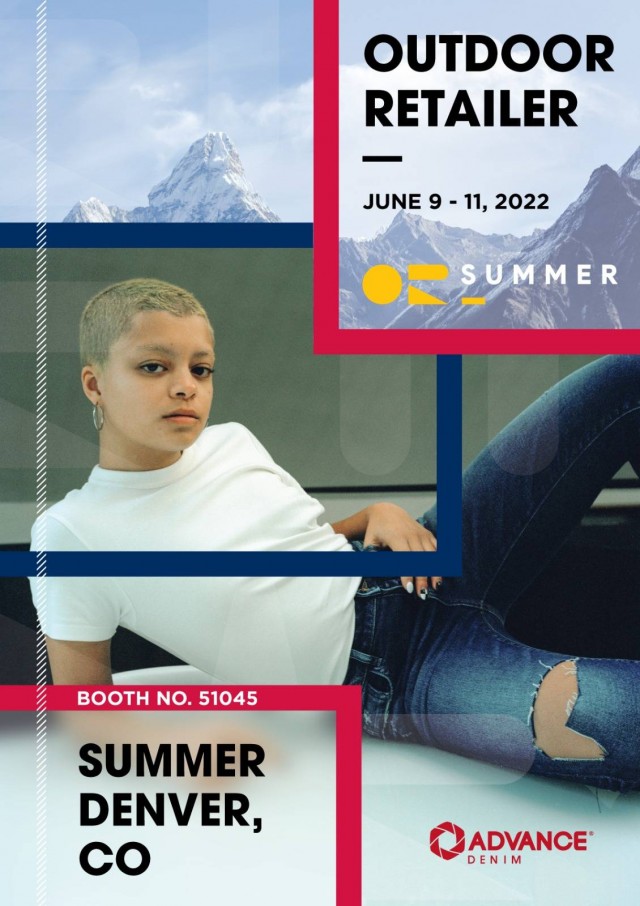
Outdoor Retailer Summer 2022 - Denver
8 June 2022
8 June 2022
Explore
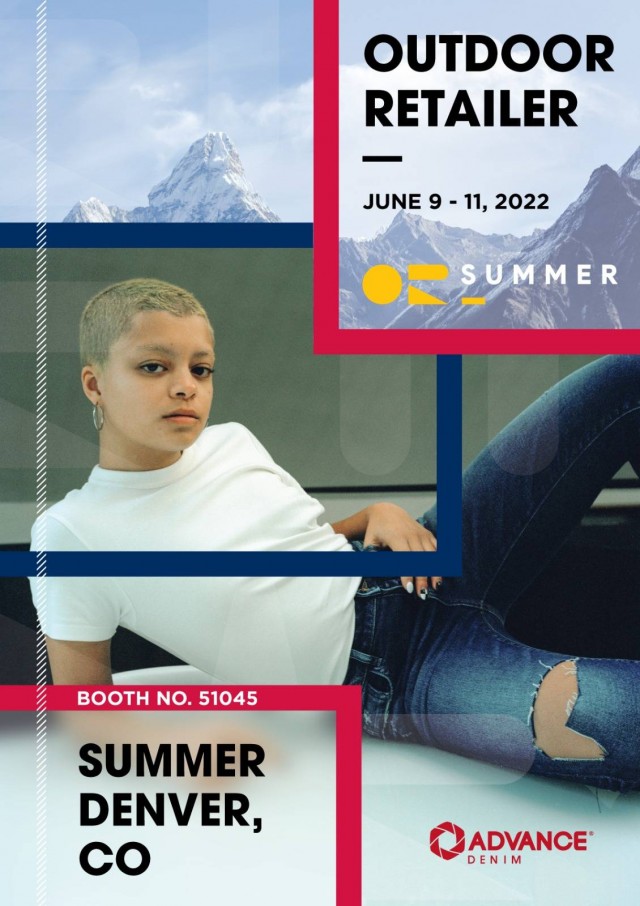
Outdoor Retailer Summer 2022 - Denver
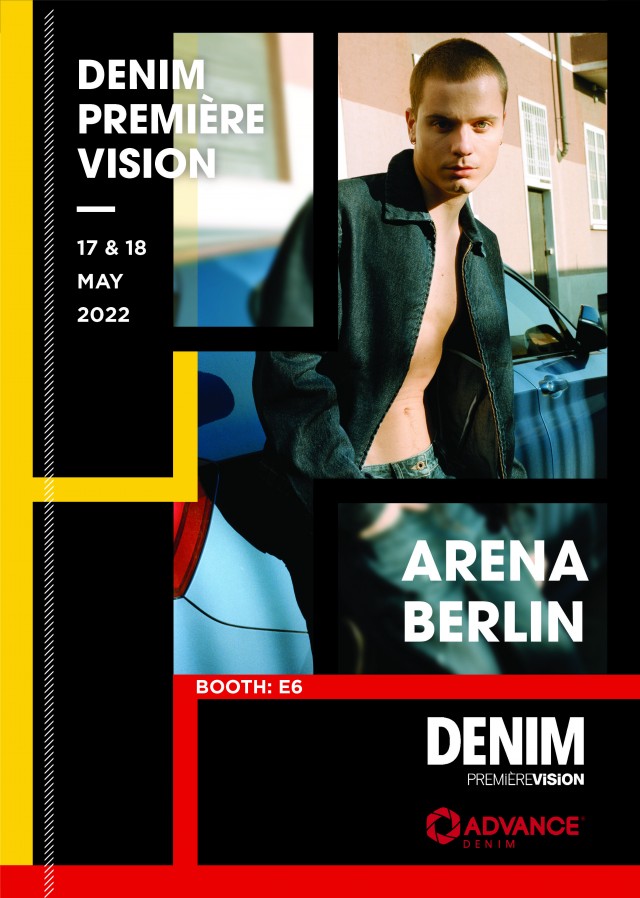
Denim Première Vision Show in Arena Berlin
14 May 2022
14 May 2022
Explore
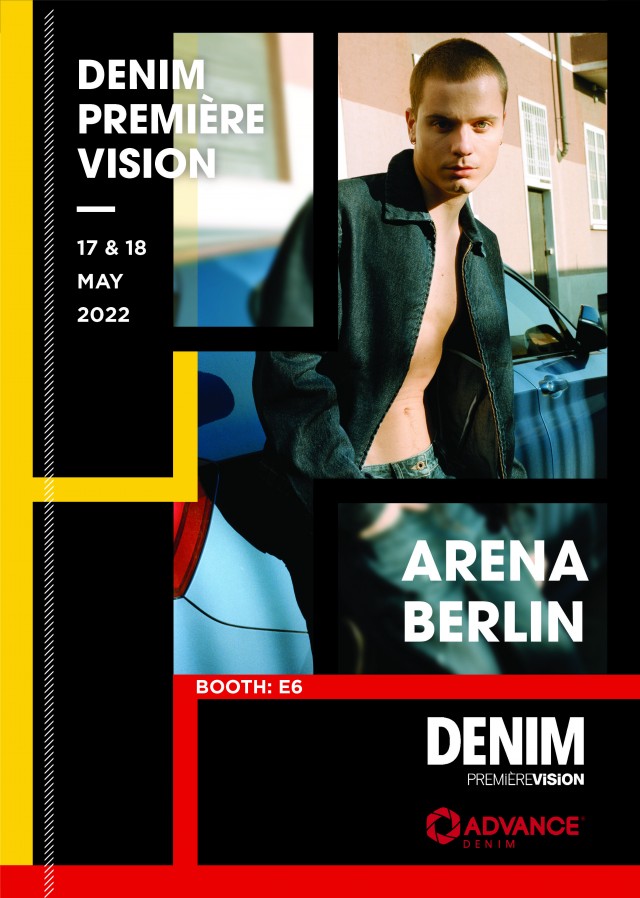
Denim Première Vision Show in Arena Berlin
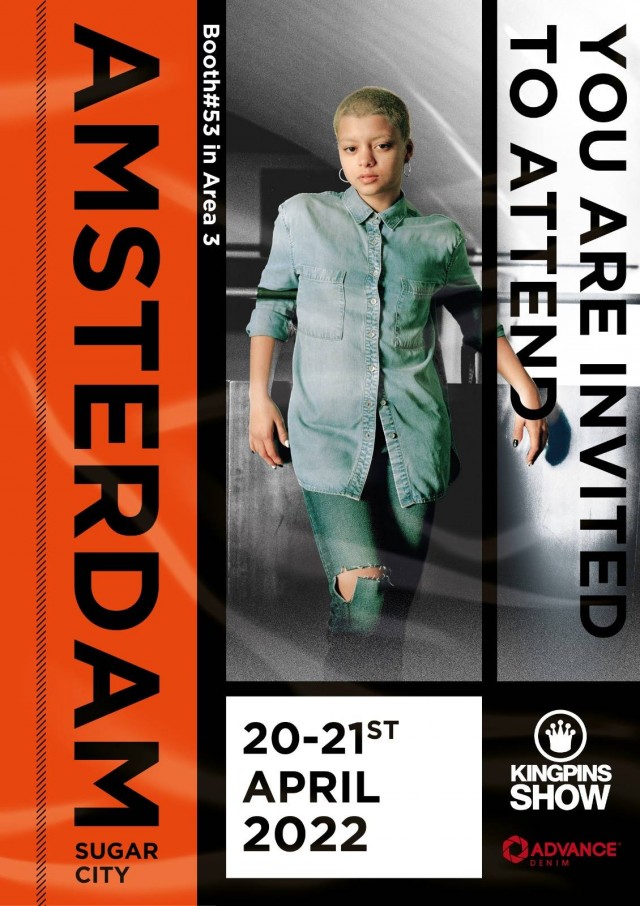
Kingpins Show in Amsterdam
20 April 2022
20 April 2022
Explore
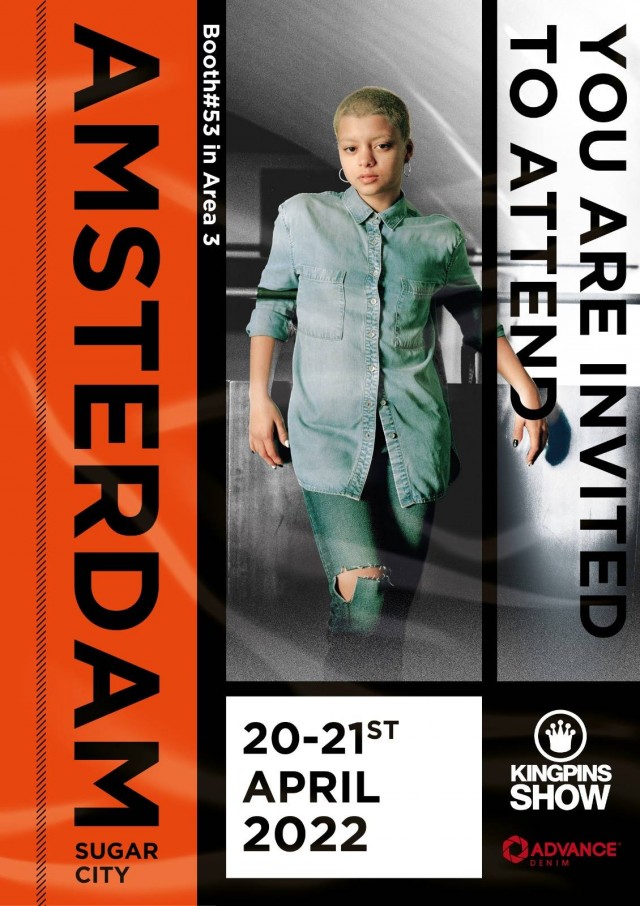
Kingpins Show in Amsterdam
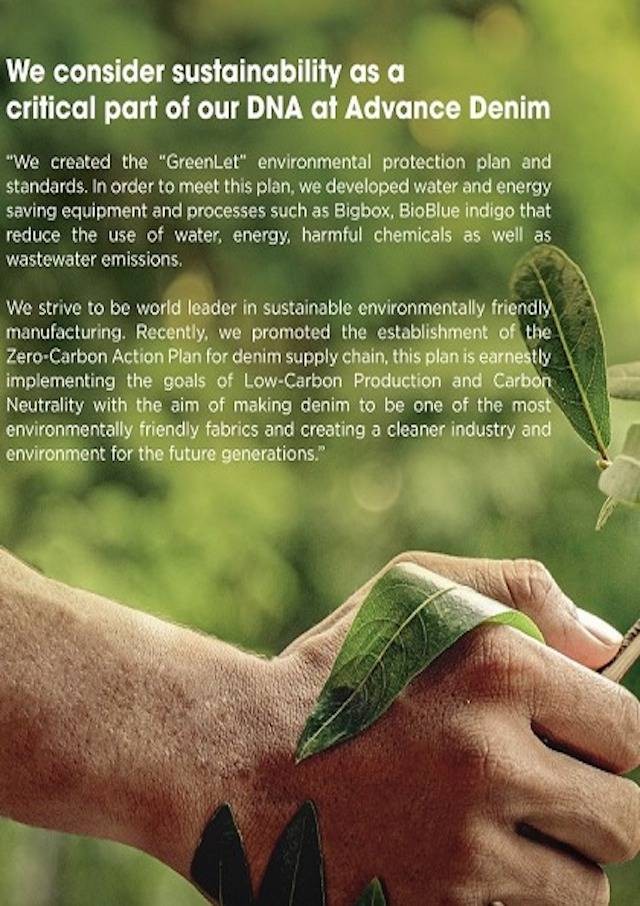
ADVANCE DENIM ESTABLISHES 10-YEAR CARBON REDUCTION PLAN
1 October 2021
1 October 2021
Explore
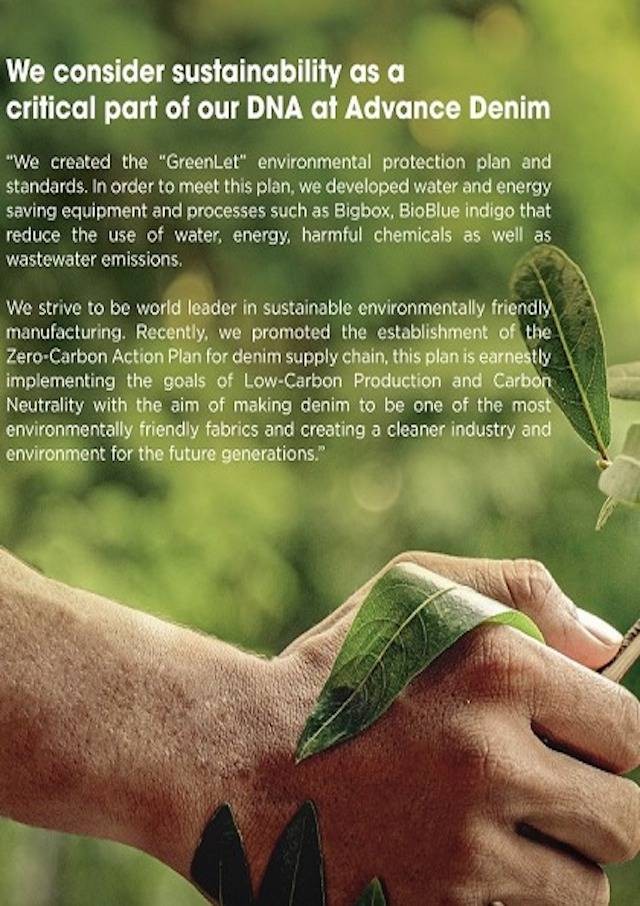